Strategies for Crafting an Effective Stock Planner
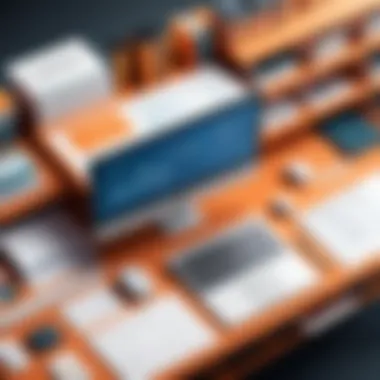
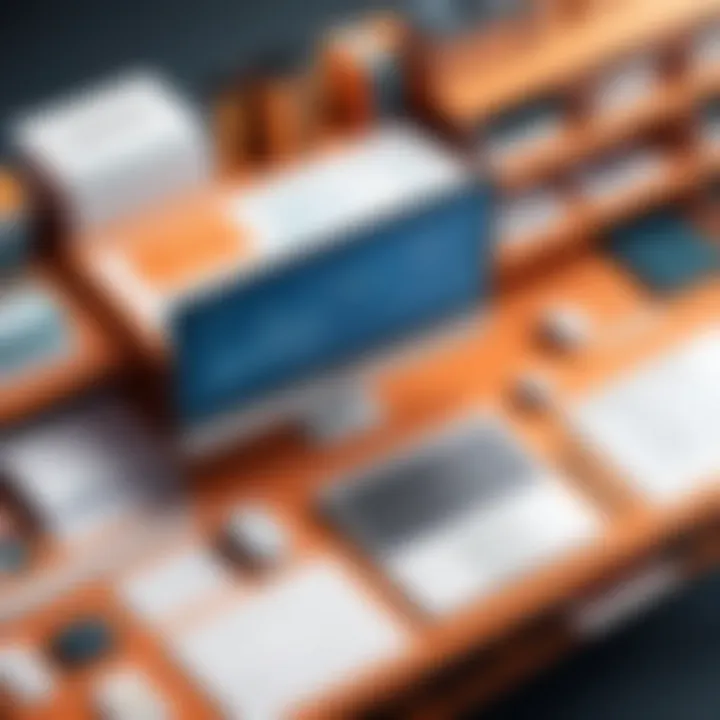
Intro
In the world of inventory management, having a reliable stock planner isn’t just a luxury; it's a necessity. As businesses grow, so does the complexity of their inventory needs. Efficient stock planning empowers organizations to maintain optimal inventory levels, ensuring that they can meet customer demands without overinvesting in stock that might never see the light of day. This section introduces the essential ideas and strategies that will shape your understanding of effective stock planning, emphasizing methods that meld well with both small and large enterprises.
Beyond the basics, it’s crucial to also consider the software solutions available that can streamline the stock planning process. Technology, when utilized correctly, can transform disarray into order, and help businesses make informed decisions backed by data. Manufacturers, retailers, or tech enterprises—whatever your field—having the right tools can often make the difference. The following sections will explore specific software relevant to stock planning, examining their functionalities and benefits comprehensively.
Understanding Stock Planning
Stock planning is like the backbone of inventory management, providing structure and direction to an often chaotic process. Without a clear understanding of stock planning, organizations may encounter inefficiencies, excess costs, and disruptions in service to their customers.
An effective stock planner serves as a blueprint for managing goods through various stages—from procurement to storage and distribution. But what does this really entail? First and foremost, stock planning hinges on accurate data collection and deep analysis of inventory patterns, customer preferences, and market trends.
Definition and Importance
The term stock planning refers to the strategies and practices that organizations utilize to determine how much inventory to maintain and when to replenish it. This process is vital for several reasons:
- Cost Management: By understanding stock levels and order cycles, businesses can avoid both overstock situations, which lead to waste, and stockouts, which can result in lost sales.
- Resource Allocation: It allows firms to allocate resources more effectively, ensuring that the right amount of product is available exactly when it’s needed.
- Customer Satisfaction: A carefully crafted stock planning strategy enables companies to fulfill orders promptly, enhancing customer satisfaction and loyalty.
"An efficient stock planner is not just about quantity; it’s about having the right product at the right time and place to meet customer needs, without missing a beat."
This definition goes beyond mere numbers; it incorporates a strategic vision crucial for growth in any business context, small or large. Companies that grasp the importance of stock planning are much likelier to streamline their processes, reduce operating costs, and ultimately increase their bottom line.
Key Objectives of Stock Planning
Diving deeper into stock planning, we can identify several key objectives that ensure success:
- Forecasting Demand: Understanding how to predict future needs based on historical data is fundamental in stock planning.
- Maintaining Inventory Levels: A well-defined system allows for the maintenance of optimal stock levels to meet demand without excess.
- Enhancing Visibility: Ensuring that stakeholders can access real-time data regarding inventory levels, which aids in quicker decision-making and responsiveness to changes.
- Minimizing Stock Holding Costs: This involves analyzing holding costs versus order costs to achieve an economical balance.
In crafting an effective stock planner, focusing on these objectives can guide organizations toward a robust framework that not only anticipates future needs but also adapts to the dynamic nature of markets.
The Components of an Effective Stock Planner
Creating an effective stock planner is not just a matter of throwing numbers around; it’s about harmonizing various components that work together to enhance the efficiency of inventory management. A well-structured stock planner ensures that a business has the right products in the right quantities at the right time. Failing to get this right can lead to excess inventory that tags along like a dog with a broken leg, or a shortage that makes the operations resemble a frantic game of musical chairs.
Understanding these components is crucial for organizations, whether they're small shops or large enterprises, aiming to optimize their inventory flow. Specifically, there are three principal components to examine: Stock Requirements Assessment, Demand Forecasting Techniques, and Inventory Level Optimization.
Stock Requirements Assessment
The basis of any good stock planner is the assessment of stock requirements. Essentially, this means figuring out what kinds of products are needed, in what quantities, and the timing of the need. This step lays the groundwork, just like a solid foundation before building a house.
To start this process, businesses should:
- Identify the product categories: For example, do you need raw materials, finished goods, or consumables?
- Analyze historical data: Look back at sales records, seasonal trends, and supply cycles to gauge future needs.
- Collaborate with sales teams: Their insights on customer preferences and purchasing patterns can steer your assessment in the right direction.
A precise evaluation allows businesses to dodge the bullets of underordering or overstocking, ultimately streamlining the entire inventory process.
Demand Forecasting Techniques
Once stock requirements are assessed, the next step is to harness demand forecasting techniques. These techniques are like a crystal ball that allows businesses to anticipate future stock needs based on various factors. Without it, one might find themselves navigating through murky waters, unsure of what lies ahead, often leading to poor decisions.
Several methods can be employed to forecast demand:
- Quantitative methods: These use numerical data from historical sales to predict future demand. Simple moving averages and exponential smoothing are part of this category.
- Qualitative methods: These involve market research, surveys, and expert opinions to gauge potential sales. It’s a bit like asking your neighbor what they might buy on Black Friday.
- Time-series analysis: This focuses on data collected at regular intervals to identify trends.
Effective demand forecasting is not just about looking at what’s sold before; it’s about understanding underlying patterns and adjusting strategies accordingly.
By adopting these techniques, businesses become adept at anticipating changes in customer preferences or external factors, thereby aligning stock levels more closely with demand.
Inventory Level Optimization
Inventory level optimization is where the rubber meets the road. It encompasses maintaining stock levels that are neither too high nor too low, ensuring that capital isn’t being wasted on excess stock, or worse yet, that customers aren't left disappointed by stock-outs.

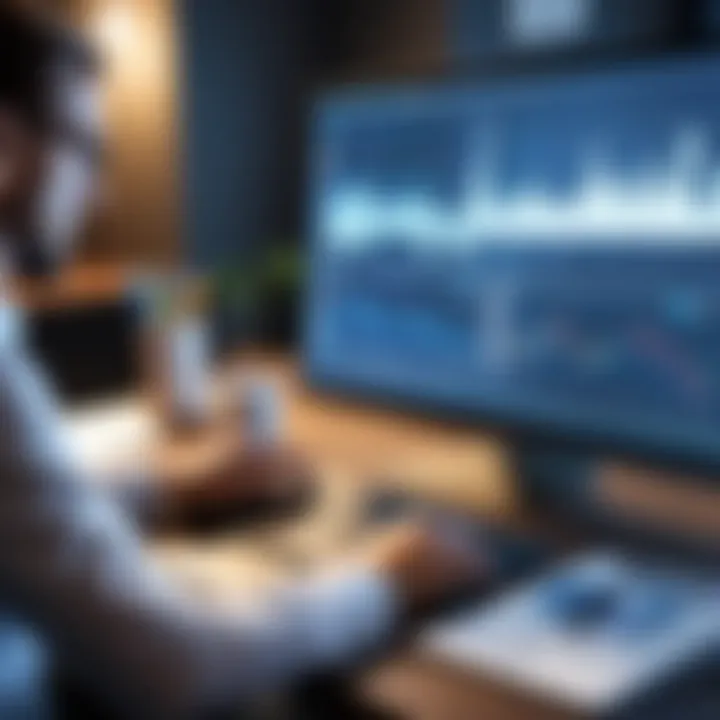
Strategies for optimizing inventory levels include:
- Setting minimum and maximum stock levels: Establish thresholds to guide reorder decisions, reducing the likelihood of shortages or excess.
- Implementing reorder points: Automating reorder points based on lead times can add efficiency to the process.
- Utilizing inventory turnover ratios: This helps assess how fast stock is sold and replaced, informing whether to up or downsize stock levels.
Correctly optimizing inventory levels is akin to walking a tightrope; balance is key. Businesses can avoid the pitfalls that come with either excess stock or stock shortages, thus enhancing productivity and customer satisfaction.
In summary, the components of an effective stock planner weave a fabric that holds together the entire inventory management process. By focusing on stock requirements assessment, employing demand forecasting techniques, and optimizing inventory levels, businesses can create a robust framework for success.
Techniques for Stock Management
In the world of stock planning, the topic of Techniques for Stock Management takes center stage as it lays the foundation for effective inventory operations. Without proper stock management techniques, businesses can quickly find themselves drowning in excess stock or, conversely, facing crippling shortages. This section explores various methods that not only streamline inventory handling but also optimize resource allocation, ultimately contributing to enhanced profitability.
Just-In-Time Inventory Systems
Just-In-Time (JIT) inventory systems prioritize reduction of waste and streamline production schedules to align closely with demand. The key philosophy behind JIT is simple: receive goods only as they are needed in the production process, thus reducing inventory holding costs. By minimizing surplus inventory, companies often realize significant savings.
However, implementing a JIT system isn't without its challenges. It requires a tight coordination with suppliers and may necessitate a shift in logistics strategies. The trade-off can be worth it, particularly for companies looking to remain agile and responsive in changing markets. A closer relationship with suppliers can lead to improved lead times, thereby enhancing overall customer satisfaction due to faster service.
Some considerations for JIT implementation include:
- Establishing robust relationships with suppliers.
- Utilizing technology for real-time inventory updates.
- Regularly assessing demand trends to adjust orders.
ABC Analysis for Prioritization
ABC Analysis is a technique used to categorize inventory into three distinct classes: A, B, and C. This method allows businesses to prioritize their stock management efforts based on the value and turnover rate of the items. "A" items are typically high-value products with a low frequency of sales, while "C" items are low-value products that are sold more frequently.
The real beauty of ABC Analysis lies in its ability to direct attention where it counts most. By focusing resources on A items, businesses can ensure that they do not run out of essential products while also keeping an eye on managing C items efficiently. For many, this method turns stock management from guesswork into a science, sharpening decision-making processes and increasing operational efficiency.
Key steps in conducting ABC analysis include:
- Assessing inventory turnover rates.
- Determining value contribution of each item.
- Classifying items into A, B, or C categories.
Safety Stock Calculations
Safety stock serves as a vital buffer in stock management. It acts as a safeguard against sudden spikes in demand or unexpected supply chain disruptions. Calculating safety stock involves understanding both the uncertainty in demand and lead times for replenishment. An appropriate safety stock level helps businesses maintain a seamless flow of operations.
There are a few different methods for calculating safety stock. Here are two common approaches:
- Statistical Approach: This involves analyzing historical sales data to predict fluctuations and using formulas from statistical models to determine appropriate safety levels.
- Fixed Method: Some businesses prefer to keep a set quantity of safety stock based on their experience and needs, which simplifies the process but may not always provide the best cushion.
When implemented correctly, safety stock can lead to smoother operational stability. However, it’s crucial to strike a balance; too much safety stock can lead to increased holding costs, while too little might result in stockouts.
Effective stock management is not just about inventory levels but understanding the delicate dance between demand forecasting and supply chain logistics.
In summary, mastering techniques for stock management—whether through JIT systems, ABC analysis, or safety stock calculations—requires a nuanced approach and constant adaptability. As businesses evolve, so too must their strategies to remain effective and competitive.
Tools and Software for Stock Planning
In the realm of stock planning, having the right tools and software is like having a trusty compass in uncharted territory. These systems not only simplify complex processes but also enable businesses to make informed decisions that can enhance efficiency and cut costs. The strategic integration of effective stock planning tools leads to better inventory management which ultimately drives profitability.
Inventory Management Software Features
When selecting inventory management software, one must keep an eye out for features that really deliver. A robust system should offer:
- Real-time Tracking: This is crucial for maintaining an accurate overview of stock levels. Real-time updates help avoid the discomfort of unexpected stockouts or excess stock, allowing businesses to react swiftly to demand fluctuations.
- Automated Reordering: This feature can save a significant amount of time. By setting minimum stock thresholds, software can automatically trigger orders whenever stock dips below a predetermined level. It’s like having a personal assistant who knows just when to ring up suppliers.
- Reporting and Analytics: Access to comprehensive reporting tools allows businesses to analyze sales trends, track inventory turnover, and forecast future demand. Being able to sift through data insights can enhance decision-making capabilities greatly.
- Multi-location Management: For companies operating across various sites, maintaining proper oversight can get tricky. A good software tool facilitates centralized control over inventories in multiple locations, providing clarity and fostering streamlined operations.
Comparative Analysis of Stock Planner Tools
The market is teeming with stock planner tools, each boasting unique features and capabilities. Conducting a comparative analysis can be the difference between selecting the right fit and facing pitfalls later on. Key factors to consider include:
- Usability: A user-friendly interface makes onboarding easier and minimizes training time, which is especially important for teams that may not be technically inclined.
- Customization Options: Different industries have varying stock management requirements. A versatile tool that caters to specific business needs enhances workflow and adaptability.
- Integration Capability: Look for software that plays nicely with existing systems, especially ERP platforms. A seamless integration can streamline processes considerably and help maintain data integrity across systems.
- Cost-effectiveness: Consider not just the upfront costs but also the potential ROI. Evaluate whether a tool can save labor hours, reduce waste, or optimize ordering processes long-term.
Exploring community reviews and discussions on platforms like reddit.com can provide real-world feedback and insights into user experiences with various tools, aiding in making well-informed decisions.
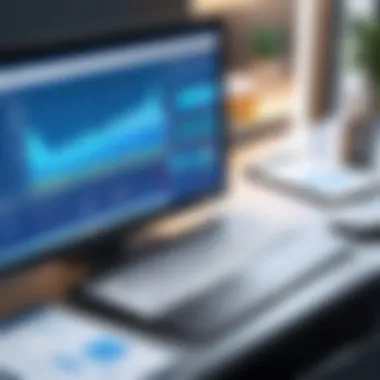
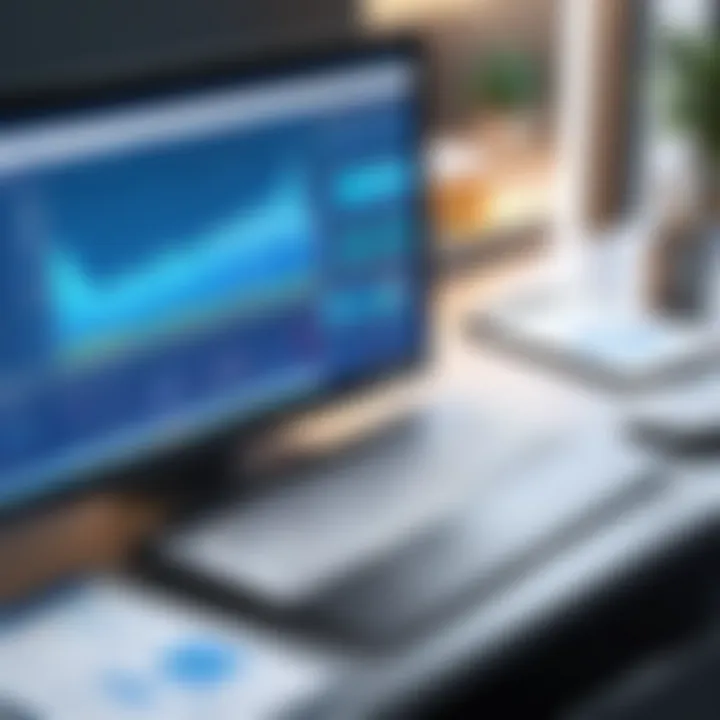
Integrating Stock Planners with ERP Systems
The synergy between stock planners and ERP systems is a match made for efficiency. An integrated approach allows for consolidated data management, which enhances various aspects of business operations:
- Streamlined Processes: With both systems in sync, data flows seamlessly, reducing redundant manual entries and the potential for errors. This keeps everything running smoothly and efficiently.
- Holistic View of Operations: Integrating stock planners with ERP systems creates a comprehensive overview of inventory levels, customer orders, and overall supply chain status, empowering managers with actionable insights.
- Enhanced Forecasting: Having access to accurate data from both stock and sales can provide more precise forecasts, allowing businesses to anticipate needs, allocate resources better, and manage cash flow effectively.
Considerations for successful integration may include assessing the compatibility of existing infrastructure and understanding what data points should be shared between the systems. By doing so, a business can maximize the benefits of both software solutions while minimizing operational hiccups.
Data-Driven Decision Making
In today's fast-paced business landscape, relying on gut feeling or previous experiences to make decisions about inventory isn't just outdated; it can be downright risky. Data-driven decision making is pivotal for crafting an effective stock planner. By harnessing data, businesses can streamline operations, respond swiftly to market changes, and minimize waste, enhancing overall efficiency.
Data-driven approaches facilitate the analysis of vast information sets, allowing planners to identify patterns and trends that may not be obvious at first glance. Using these insights, companies can predict demand more accurately and adjust their inventory accordingly. Without such an approach, organizations are like ships lost at sea, without a navigational chart to guide them.
Utilizing Business Intelligence
Business intelligence (BI) tools gather, process, and analyze large volumes of data, turning it into actionable insights. They are crucial for stock planners who aim to make informed decisions. With BI, stock planners can visualize trends, monitor inventory levels, and track customer buying habits. For instance, a retail business might utilize tools like Tableau or Power BI to create dashboards that provide real-time updates. This immediacy helps in quickly spotting declining stock items that may need replenishment or promotional efforts.
Implementing BI solutions can lead to significant improvements in operational efficiency, such as:
- Improved Forecast Accuracy: Advanced algorithms analyze historical data and predict future trends.
- Enhanced Reporting: Customizable dashboards provide clarity at a glance.
- Strategic Insights: Access to competitive analysis and market trends aids decision-making.
Effective use of BI can transform data into a strategic asset, driving informed decision-making that enhances stock management practices.
Forecasting Models and Their Applications
Forecasting models serve as the backbone of data-driven decision making in stock planning. These mathematical tools use historical data to predict future demand. Among the commonly used models are:
- Time Series Analysis: It examines historical patterns over regular intervals, making it suitable for businesses with consistent demand trends.
- Regression Analysis: This method assesses the relationship between various factors, such as price changes and product demand.
- Machine Learning Models: These algorithms learn from data and improve their predictions over time, allowing for very sophisticated demand forecasting.
The choice of model often depends on the nature of the business and the type of data available. For example, a seasonal toy store might lean on time series methods, while a tech gadget retailer may prefer regression, taking into account new technology releases.
Analyzing Trends in Sales Data
Analyzing sales data is another critical facet of data-driven decision making. It's not enough to just collect figures; one must also interpret them. Key areas to focus on include:
- Customer Purchasing Patterns: Understanding what, when, and why customers buy can refine stock strategies and improve marketing efforts.
- Identifying Stock-Outs: By reviewing sales patterns, stock planners can mitigate the risk of running out of popular items before peak demand periods.
- Sales Correlations: Observing how changes, such as promotional activities or competitor pricing, impact sales can help refine inventory strategies.
Tools like Google Analytics or specific CRM systems can provide deep insights into these patterns. Crafting a responsive stock plan hinges on recognizing and calculating these trends accurately, ensuring the business remains agile in its market approach.
Challenges in Stock Planning
Stock planning, while crucial for operational efficiency, is not without its challenges. Understanding these challenges can help businesses mitigate risks, improve efficiency, and enhance overall performance. When stock planning is executed poorly, it can lead to cascading issues that affect both the organization and its customers. This section delves into the common pitfalls, supply chain disruptions, and balancing stock levels with customer demand—each a significant aspect for the effective stock planner.
Common Pitfalls and Errors
Navigating stock planning can be tricky, and errors often arise due to a variety of reasons. For instance, a lack of updated data can lead to overstocking or stockouts. This can create a bottleneck in sales as well as increased holding costs for excess inventory.
Furthermore, failure to properly categorize products can cause misallocations in stock prioritization. For example, treating high-demand items the same as seasonal ones may result in missed opportunities for sales during peak periods. Companies must implement regular inventory audits to catch discrepancies early and adjust stock levels accordingly.
- Poor Forecasting: Assuming that previous trends will continue without accounting for external factors often leads to inaccurate demands.
- Underestimating Lead Times: Not accounting for longer lead times from suppliers can create shortages.
- Ignoring Changing Consumer Preferences: Market trends shift, and failing to adapt can leave inventory stale.
"Mistakes in stock planning are like a snowball rolling downhill; what starts small can turn into an avalanche of issues if not addressed promptly."
Dealing with Supply Chain Disruptions
Supply chain disruptions have become a common topic in today's global market. With events like pandemics, natural disasters, or political instability, businesses must prepare for the unexpected. Disruptions can lead to delayed shipments or even a complete halt in production, which can severely affect stock levels.
To mitigate these challenges, it’s vital to maintain a diversified supplier base. Relying on a single source can leave a company vulnerable to disruptions. Additionally, adopting technology that provides real-time supply chain visibility allows better planning and faster responsiveness.
- Develop Contingency Plans: Have alternative suppliers lined up.
- Monitor Supplier Performance: Build relationships with suppliers and assess their reliability regularly.
- Use Technology: Advanced analytics can predict potential disruptions and suggest corrective measures before issues arise.
Balancing Stock Levels with Customer Demand
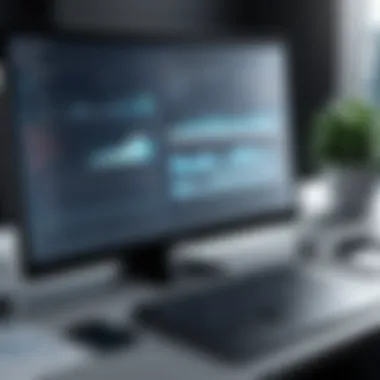
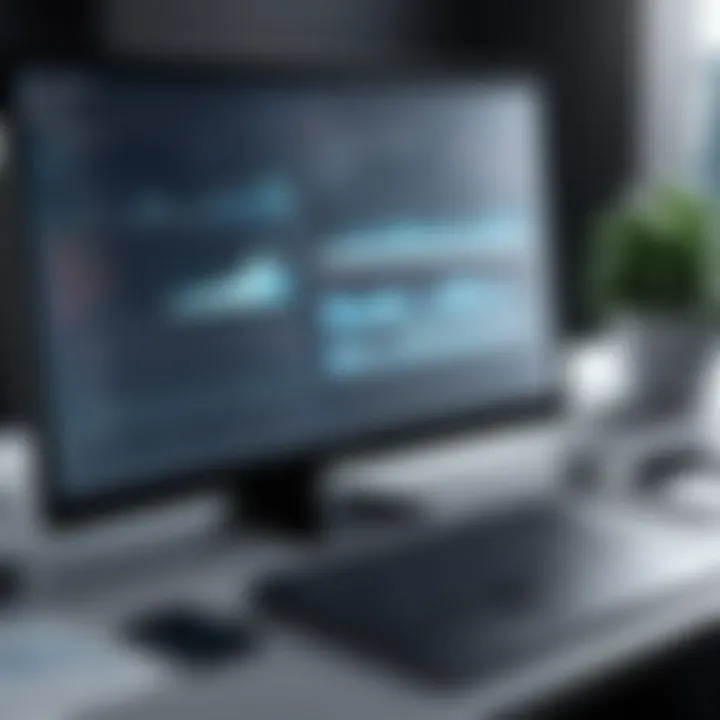
Finding the sweet spot between having enough stock for customer demand while not overcommitting funds to inventory is a daunting task for stock planners. Too much stock ties up capital, while too little leads to hurried replenishments and missed sales.
Effective techniques include:
- Conducting Regular Demand Forecasting: Utilize historical data alongside market research to anticipate customer needs accurately.
- Implementing Flexible Stock Policies: Adjust stock levels based on changing demand patterns, which can help to reduce waste and increase turnover rates.
- Gathering Customer Feedback: Direct input from customers can provide insight into preferences and upcoming trends.
By keeping tabs on customer behavior and market fluctuations, stock planners can react swiftly, ensuring they meet customer expectations without drowning in excess inventory.
Best Practices for Stock Planners
In the world of stock planning, a series of best practices enables both small and large businesses to maintain operational efficiency and an edge over competitors. Implementing these practices is not just about following a checklist; it's akin to crafting a symphony where each element harmonizes with the other to produce an efficient whole. By adopting these best practices, organizations can enhance their decision-making processes, improve their inventory management systems, and ultimately drive profitability.
Regular Inventory Audits
Conducting regular inventory audits is a cornerstone of effective stock planning. Just as a ship must be regularly checked to avoid leaks, inventory needs consistent surveillance to ensure accuracy. These audits help verify that inventory records match physical stock levels, reducing discrepancies caused by theft, damage, or simple human oversight.
The benefits of performing these audits are clear:
- Accuracy Improvement: By regularly comparing physical counts to system records, businesses can identify errors and adjust them swiftly.
- Waste Reduction: Spotting obsolete or slow-moving items during audits allows for more informed decisions about markdowns or discontinuation.
- Enhanced Cash Flow: Better inventory control means less capital tied up in excess stock, improving liquidity.
Regular audits can often highlight trends that might not be visible in day-to-day operations.
Incorporating technology, such as barcode scanning or RFID tags, can make the audit process more efficient. This technology translates into actionable data, allowing managers to focus on optimizing inventory levels.
Collaboration Across Teams
Effective stock planning is rarely a solo endeavor. Collaboration among departments—such as procurement, sales, and finance—can significantly improve the stock management process. Each team brings unique insights that can inform better decision-making. For instance:
- Sales Forecasting: The sales team can provide real-time feedback on customer preferences, which can drastically alter purchasing decisions.
- Procurement Input: The procurement team can share lead times and vendor reliability, allowing for smarter stocking recommendations.
- Financial Oversight: Understanding cost implications from the finance team helps to make stock decisions that align with the organization’s budgetary constraints.
Collaboration fosters a culture of transparency, where each department understands the integral role they play in effective stock management. Encouraging regular interdepartmental meetings can help address any cross-functional challenges.
Consistency in Assessment Metrics
Consistency in metrics lets businesses build a reliable framework for stock planning. When assessing inventory performance, utilizing uniform metrics across all departments ensures that data is comparable and actionable. Here are several critical considerations:
- Key Performance Indicators (KPIs): Establish KPIs such as inventory turnover rates, days sales of inventory, and carrying costs. These should be standardized across the business.
- Data Integrity: Ensuring that the same data sources are used for decision-making minimizes confusion and inconsistency.
- Benchmarking: Companies should regularly compare their metrics against industry standards to assess their performance, ensuring they remain competitive.
While it may seem tedious, the practice of using consistent assessments allows an organization to make informed, data-driven decisions that directly address stock management efficiency. Without these measures, decision-making can quickly become erratic and subjective, which is detrimental to long-term success.
By embracing these best practices for stock planning, companies can navigate the complexities of inventory management more effectively. Establishing a methodical approach not only enhances operational workflows but also sets a solid foundation for adapting to future challenges in stock management.
Future Trends in Stock Planning
The landscape of stock planning is evolving faster than ever, with an array of shifts poised to redefine how businesses manage their inventory. As organizations strive for greater efficiency and responsiveness in an unpredictable market, understanding these future trends is crucial. Embracing these emerging changes not only equips businesses to navigate challenges but also positions them to leverage opportunities that may arise. The integration of cutting-edge technologies, the influence of artificial intelligence, and a greater focus on sustainability practices are all reshaping stock planning. Below, we explore these essential elements.
Emerging Technologies in Inventory Management
In today’s rapidly shifting environment, emerging technologies in inventory management are beginning to play a vital role in stock planning. Various technologies, from IoT devices to advanced data analytics platforms, are no longer just optional but essential tools for successful inventory management.
- IoT Sensors: The Internet of Things is making its mark by allowing real-time tracking of inventory levels. By using sensors fitted on products or pallets, businesses can instantly monitor stock levels and movements. This leads to improved visibility across the entire supply chain.
- Blockchain: This technology enhances transparency in the inventory process. By securing transactions on a decentralized ledger, businesses can trace products back to their origins and track supply chain shifts with unmatchable accuracy.
- Cloud Computing: Leveraging cloud storage means that data accessibility reaches new heights. It allows for collaborative access among team members across various locations. The agility provided by cloud solutions enables quicker decision-making and better responsiveness to market changes.
Overall, integrating these technological advancements not only streamlines inventory processes but also opens the door to significant cost savings and operational efficiencies.
The Impact of Artificial Intelligence
Artificial intelligence has already started reshaping the landscape of stock planning. Its ability to analyze massive datasets far exceeds human capabilities, thus offering insights that drive smarter decision-making. Here are key ways AI impacts this field:
- Predictive Analytics: AI can forecast trends and predict stock requirements based on historical data. This means businesses can maintain optimal stock levels and avoid overstocking or stockouts.
- Automated Replenishment: With AI algorithms continuously assessing stock levels, businesses can automate the replenishment process. This minimizes manual intervention, making the system more efficient.
- Enhanced Customer Insights: AI tools can analyze customer behavior to predict preferences and demand patterns. By aligning the stock with customer needs, businesses can improve sales and customer satisfaction.
Incorporating AI into stock planning leads to a proactive rather than reactive approach, fostering a culture of continuous improvement and adaptability.
Sustainability Practices in Stock Planning
In recent years, sustainability has taken center stage in business strategies. Companies are not just responsible for profits anymore; they are increasingly accountable for their environmental impact. In stock planning, here’s how sustainability practices are influencing operations:
- Eco-Friendly Products: Adopting sustainable products leads to responsible sourcing. Businesses are incorporating more eco-friendly materials while monitoring their suppliers’ practices to ensure ethical sourcing.
- Waste Reduction: Efficient inventory practices can significantly reduce waste. By applying just-in-time principles and accurate demand forecasting, organizations can minimize excess stock and spoilage.
- Carbon Footprint Optimization: Companies are using data analysis tools to assess and optimize their carbon footprints. This involves reviewing their logistics and transportation methods to implement greener alternatives.
Sustainability practices in stock planning not only resonate with environment-conscious consumers but also cultivate brand loyalty and provide a competitive edge in an increasingly eco-aware market.