Enhancing Supplier Collaboration with SAP Solutions
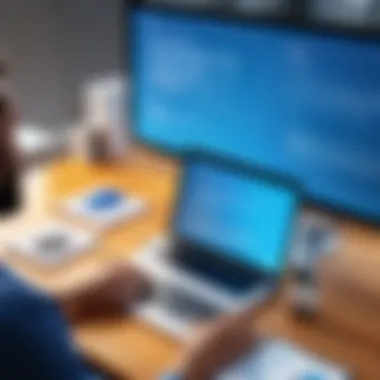
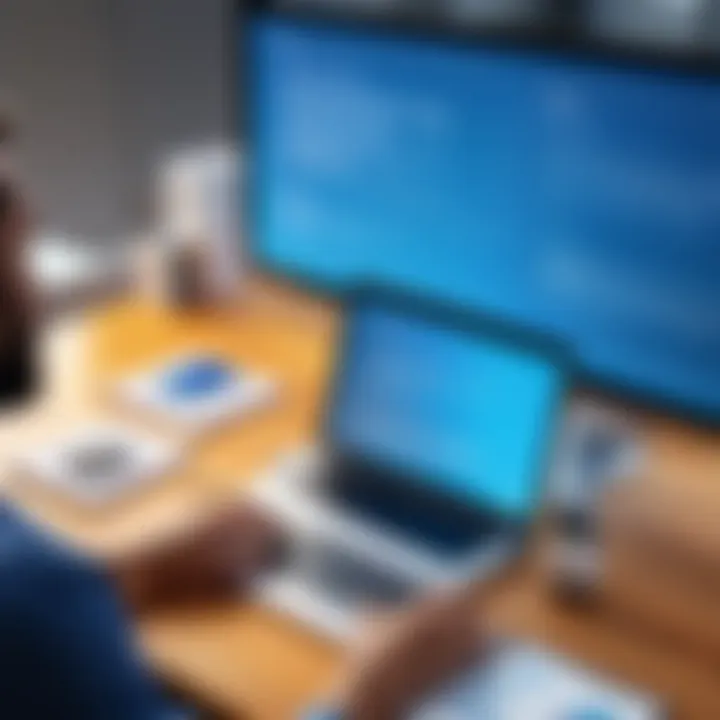
Intro
In today's complex business landscape, strong supplier relationships are crucial for achieving operational success. Effective collaboration with suppliers can lead to improved product quality, reduced costs, and enhanced innovation. As a cornerstone in enterprise resource planning, SAP solutions play a significant role in fostering supplier collaboration. Understanding how to leverage these tools can transform how organizations engage with their suppliers and streamline the overall supply chain process.
The article delves into the capabilities of SAP software that enhance supplier collaboration. Through an analysis of various functionalities and case studies, we will explore actionable strategies that can optimize supplier relationships. Integrating supplier insights into strategic decision-making becomes not just advantageous, but essential. This journey will provide valuable insights for IT professionals and business leaders who seek to enrich their operational efficiency through better supplier relationships.
Overview of Software
Description of Software
SAP offers a suite of solutions designed to streamline business processes including those related to supplier management. These solutions aim to facilitate collaboration, enhance data visibility, and promote effective communication within the supply chain ecosystem. Tools such as SAP Ariba and SAP S/4HANA play pivotal roles in fortifying supplier relationships by automating key tasks and providing real-time insights.
Key Features
SAP's supplier collaboration tools boast a variety of features:
- Supplier Relationship Management: Tools to manage supplier interactions effectively.
- Real-time Analytics: Instant data insights that optimize decision-making.
- Integrated Communication Channels: Facilitating seamless interaction between buyers and suppliers.
- Procurement Automation: Streamlining purchasing processes to reduce time and effort.
- Compliance Tracking: Ensuring compliance facilitates trust and reliability in supplier relationships.
These features empower businesses to cultivate robust partnerships, leading to shared success and continual improvement in operational processes.
Supplier Collaboration Effectiveness
Understanding the effectiveness of supplier collaboration is vital for any organization seeking improvement.
Measuring Collaboration Efficacy
Success in supplier collaborations can be assessed through several metrics:
- Delivery Performance: Timeliness and accuracy of deliveries.
- Quality Metrics: Evaluation of products received in terms of standards.
- Cost Management: Monitoring cost savings achieved through collaboration.
Instituting a framework for measuring these aspects ensures that businesses can track progress and make necessary adjustments.
Successful Case Studies
Several organizations have harnessed SAP solutions to enhance supplier collaboration effectively:
- Walmart: Leveraged SAP Ariba for efficient supplier management and better inventory control.
- Siemens: Utilized SAP S/4HANA to optimize communication with suppliers, resulting in improved turnaround times.
These examples illustrate the potential of SAP solutions in transforming supplier relationships into strategic assets.
End
Supplier collaboration is no longer a secondary consideration; it is central to achieving operational excellence. By effectively leveraging SAP solutions, organizations can enhance their relationships with suppliers, improve procurement processes, and optimize supply chain efficiency. With a real-time focus on data and communication, the potential for creating value through strategic partnerships is significant. By investing in the right tools and practices, businesses can cultivate a collaborative ecosystem that leads to sustained success.
Understanding Supplier Collaboration
Supplier collaboration is a crucial component of effective supply chain management. It fosters not only business relationships but also enhances efficiency and innovation. It means working closely with suppliers to establish trust, streamline processes, and create shared goals. This collaborative approach can lead to innovative products, improved quality, and reduced costs. Understanding supplier collaboration helps organizations align with strategic goals and respond swiftly to changes in market demand.
Definition and Importance
Supplier collaboration refers to the cooperative effort between a company and its suppliers. This collaboration can encompass various activities, including joint product development, forecasting, and inventory management. The main aim is to create win-win situations where both parties benefit.
The importance of supplier collaboration lies in its capacity to drive mutual growth and enhanced operational efficiency. Companies that prioritize collaboration can access unique insights and resources from suppliers, improving competitiveness and adaptability. Furthermore, strong collaboration can lead to shared risk management. It enables businesses to navigate uncertainties collectively, thus building resilience.
Challenges in Supplier Collaboration
While supplier collaboration offers many advantages, it does not come without obstacles. Some of the challenges organizations face include:
- Communication Barriers: Misunderstandings can arise if communication is not clear or consistent. Different time zones and languages can complicate interactions, affecting relationship building.
- Cultural Differences: Different organizational cultures can create friction. Understanding and valuing each culture is essential for successful collaboration.
- Data Integration Issues: Effective collaboration requires sharing data. However, disparate systems might hinder seamless integration, making it challenging to access real-time information.
- Trust Issues: Building trust can take time. A lack of trust can lead to reluctance in sharing sensitive information, ultimately working against collaborative efforts.
The Role of SAP in Supplier Collaboration
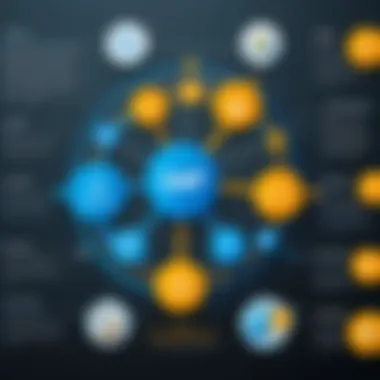
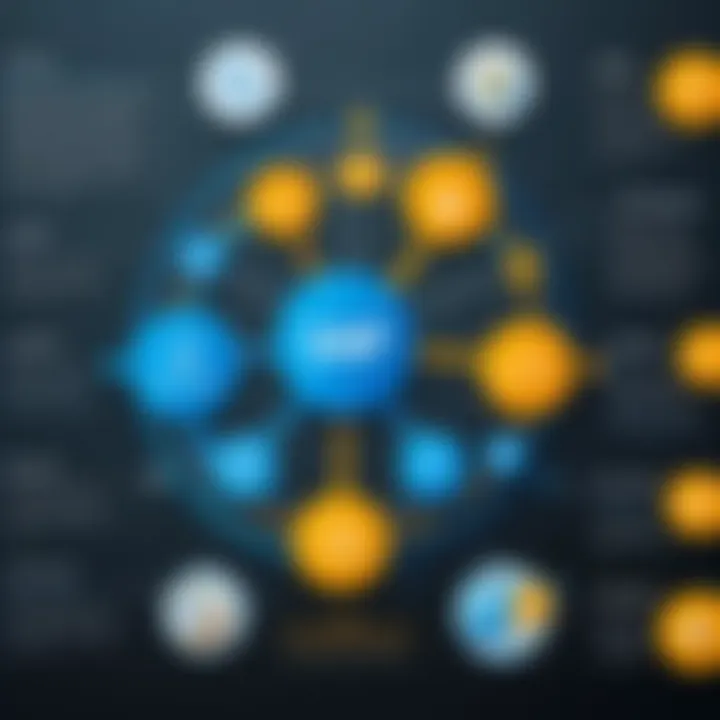
Understanding how SAP facilitates supplier collaboration is essential for organizations seeking to optimize their procurement processes. A well-integrated system can lead to enhanced communication, efficiency, and profitability. SAP provides a suite of solutions that streamline interactions between suppliers and organizations, ensuring all parties are aligned in their goals.
The importance of SAP in supplier collaboration cannot be understated. This technology aids in consolidating supplier information, monitoring performance, and establishing metrics that align with organizational objectives. As businesses increasingly recognize the significance of robust supplier relations, leveraging SAP's capabilities becomes crucial to achieving strategic goals.
Overview of SAP Solutions
SAP offers various solutions designed to enhance supplier collaboration. At its core, SAP provides tools that allow organizations to manage supplier relationships effectively, address procurement challenges, and drive operational efficiency. By implementing these solutions, businesses can significantly reduce delays, enhance data visibility, and ensure compliance with regulatory requirements. The result is a more resilient and responsive supply chain that adapts to changing market conditions.
Some specific SAP solutions include:
- SAP Supplier Relationship Management (SRM)
- SAP Materials Management (MM)
- SAP Production Planning (PP)
These tools support different aspects of collaboration, each contributing uniquely to the overall supplier management strategy.
Key SAP Modules Supporting Collaboration
Supplier Relationship Management (SRM)
Supplier Relationship Management (SRM) is pivotal in facilitating seamless interactions between organizations and their suppliers. The main characteristic of SRM is its ability to centralize supplier information and streamline procurement processes. This module fosters a collaborative environment where both suppliers and buyers work together effectively.
One unique feature of SRM is its focus on enhancing supplier performance analysis. Organizations can track supplier metrics, such as delivery reliability and quality compliance, which are crucial for maintaining strong supplier relationships. This analytical capability allows businesses to identify underperforming suppliers and make informed decisions to optimize the supply chain. Despite its benefits, organizations must consider possible integration challenges when implementing SRM with existing systems.
Materials Management ()
Materials Management (MM) plays a critical role in monitoring the flow of materials throughout the supply chain. This module is favored for its comprehensive coverage of procurement and inventory processes. One of the main strengths of MM is its real-time data analysis, which allows organizations to manage their resources more effectively and respond swiftly to market shifts.
The unique capability of MM lies in its integration with other SAP modules, ensuring a cohesive approach to supply chain management. This aspect supports effective planning and execution of procurement strategies. Advantages of utilizing MM include enhanced inventory management and reduced wastage. However, reliance on accurate data is essential for the system's effectiveness, and businesses must be prepared to maintain data quality.
Production Planning (PP)
Production Planning (PP) is integral for organizations focused on optimizing their production schedules in conjunction with supplier capabilities. The unique ability of PP is its focus on aligning production schedules with supplier deliveries, which is essential for maintaining efficiency in manufacturing environments.
A key characteristic of PP is its role in demand forecasting and capacity planning. This module enables organizations to predict product demand accurately and adjust production accordingly, ensuring that materials are available when needed. While this leads to increased operational efficiency, businesses must ensure that production plans are adaptable to unexpected changes in supply or demand. Overall, PP serves as a critical component in marrying production processes with supplier collaboration.
Analyzing the Benefits of Enhanced Collaboration
Collaboration between suppliers and organizations is essential for modern supply chain management. Understanding the specific advantages of this partnership can lead to significant improvements in operational efficiency. Enhanced collaboration allows businesses to respond more swiftly to market changes, innovate effectively, and ultimately, realize better financial outcomes. Thus, analyzing these benefits is crucial for organizations that are looking to integrate SAP solutions into their collaborative efforts.
Cost Reductions
One of the primary benefits of enhanced collaboration through SAP solutions is cost reductions. When suppliers and companies work closely together, many cost-related inefficiencies can be identified and addressed. For example, organizations can reduce procurement costs by consolidating orders and managing inventory more effectively. SAP tools enable visibility across the supply chain, which helps in forecasting needs accurately.
- By sharing data, suppliers can adjust their production schedules to match actual demands.
- This shared visibility leads to lower holding costs, as excess inventory is minimized.
- Companies often find that they can negotiate better terms with suppliers when there is transparency in pricing and inventory levels.
"Automation through SAP solutions can streamline procurement processes, reducing manual errors and resulting in significant savings over time."
Improved Supply Chain Responsiveness
Another significant benefit of effective supplier collaboration is improved responsiveness in the supply chain. With SAP solutions, organizations can receive real-time updates from suppliers regarding inventory levels, production timelines, and potential delays. This immediate feedback loop enhances the organization's ability to react swiftly to changes.
- Real-time data integration helps organizations to allocate resources efficiently and adjust plans as necessary.
- Faster communication channels minimize downtime when issues arise, enabling teams to address them promptly.
- Enhanced collaboration also supports agile methodologies, allowing for quicker product cycles and time-to-market improvements.
As a result, organizations can maintain a competitive edge in a fast-paced business environment.
Stronger Supplier Relationships
Enhanced collaboration leads to stronger relationships with suppliers. When businesses openly share information and work cooperatively, mutual trust develops. This trust is vital for long-term partnerships.
- Strong supplier relationships lead to better negotiation outcomes, as trust is built over time.
- Suppliers are often more willing to prioritize companies that they have good relationships with, ensuring reliability and preference during critical times.
- Further collaboration can drive innovation, as suppliers may be more involved in product development processes or initiatives aimed at cost reductions.
Implementing SAP for Supplier Collaboration
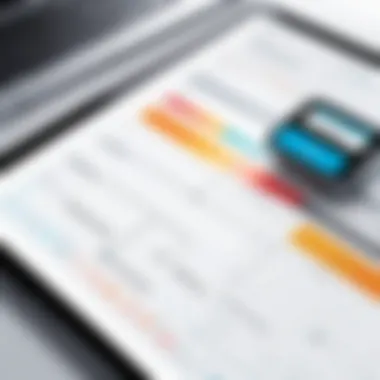
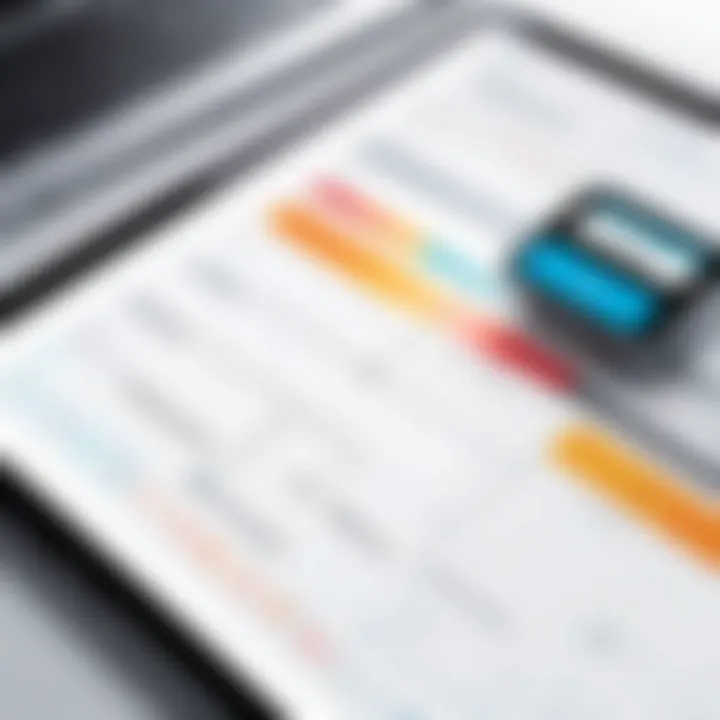
Implementing SAP for supplier collaboration is a crucial step for organizations aiming to enhance efficiency and improve relationships in the supply chain. With SAP solutions, businesses can automate processes, integrate data seamlessly, and foster collaboration with suppliers more effectively. This section will explore the vital components involved in implementing SAP solutions and how they can transform supplier interactions.
Assessment of Existing Processes
Before implementing SAP, it is essential to assess existing processes within the organization. This assessment allows for a clear understanding of how current practices function, identifying areas that require improvements or automation. Key steps in this assessment include:
- Mapping current processes: Document how supplier interactions currently occur, noting inefficiencies or bottlenecks.
- Identifying technology gaps: Recognize which parts of the current processes could benefit from SAP integration.
- Engaging stakeholders: Involve teams from procurement, IT, and operations to gather insights on current challenges.
This thorough evaluation lays a foundation for a smooth SAP integration by highlighting specific areas where the supplier collaboration can be enhanced significantly.
Integrating Supplier Data into SAP
Integrating supplier data into SAP is vital for ensuring accurate and real-time information flow between the organization and its suppliers. This aspect of implementation involves several considerations:
- Data Standardization: Ensure that data formats are consistent for smooth integration. This includes supplier contact information, pricing, delivery schedules, etc.
- Use of SAP Cloud Platform: Leverage the SAP Cloud Platform to facilitate secure data sharing and collaboration.
- API Integrations: Implement APIs to connect SAP with other systems that suppliers may use. This streamlines data exchanges.
An effective integration strategy ensures that every detail about supplier relationships is readily available, improving decision-making and operational efficiency.
Training Internal Teams
Training is a significant factor in the successful implementation of SAP solutions. Internal teams must understand how to use these systems effectively to maximize supplier collaboration. Effective training strategies include:
- Developing a training curriculum: Create courses that cover the functionalities of SAP related to supplier management.
- Engagement sessions: Conduct hands-on workshops that allow employees to practice using SAP tools in real-world scenarios.
- Ongoing Support: Establish a support system that includes access to documentation and help desk services, enabling team members to seek assistance as needed.
Investing in training not only enhances user adoption but also empowers teams to utilize SAP solutions comprehensively. This collective knowledge fosters a culture of collaboration and efficiency within the organization.
"Successful implementation of SAP requires not only the right technology but also a commitment to training and process improvement."
In summary, implementing SAP for supplier collaboration is a multifaceted process that necessitates a detailed assessment of existing operations, strategic integration of supplier data, and robust training for internal teams. This approach helps organizations fully leverage the power of SAP solutions to enhance supplier relationships and overall supply chain efficiency.
Case Studies: Successful SAP Implementations
Understanding successful implementations of SAP solutions is essential for grasping how organizations maximize supplier collaboration. Case studies provide concrete examples of practical applications, showcasing challenges, approaches, and the realized benefits of SAP integration. Such examples underline the potential effectiveness of SAP systems in increasing collaboration efficiency among suppliers and internal teams.
Analyzing case studies can also highlight key elements that contribute to successful outcomes, such as proper training, stakeholder engagement, and continuous improvement strategies. Organizations can learn what works and avoid common pitfalls by studying real-life scenarios. This examination reveals not just the 'how' but also the 'why' behind successful SAP implementations in supplier collaboration.
Global Manufacturer Case Study
A leading global manufacturer faced challenges in managing its diverse supplier base. The complexity of communication, varying standards, and inconsistent data were major obstacles in enhancing their supply chain efficiency. To tackle these issues, they implemented SAP Supplier Relationship Management (SRM).
The main features leveraged included:
- Centralized Data Management: All supplier data was unified in one platform, ensuring consistent updates and visibility.
- Supplier Performance Assessment: KPIs were established to evaluate supplier performance in real-time, enabling the manufacturer to address concerns promptly.
- Enhanced Communication: The SAP platform allowed for streamlined communication with suppliers, improving relationship management.
Post-implementation, the manufacturer reported a significant reduction in lead times by 25% and a boost in cost savings of approximately 15%. The seamless integration of supplier data within SAP facilitated better decision-making and strengthened partnerships, demonstrating the value of effective collaboration.
Retail Chain Case Study
A prominent retail chain sought to improve its responsive capability to market demands and customer preferences. The organization faced challenges in inventory management and supplier engagement, leading to stockouts and customer dissatisfaction. To resolve these issues, they adopted SAP Materials Management (MM) and Production Planning (PP) modules.
Key strategies included:
- Real-Time Inventory Tracking: The SAP MM module provided real-time visibility into inventory levels across various locations.
- Demand Forecasting: Using SAPβs analytical tools, the chain could predict demand patterns, significantly enhancing replenishment strategies.
- Supplier Collaboration Framework: Enabling suppliers to access relevant inventory data fostered a joint planning environment.
The outcome was impressive. The retail chain achieved a 30% improvement in inventory turnover and reduced operational costs by 20%. Furthermore, supplier relationships matured as they worked collaboratively within the SAP framework, underscoring how integrated systems can drive mutual benefits across the supply chain.
Measuring Collaboration Success
Measuring success in supplier collaboration is a critical aspect of ensuring the effectiveness of implemented strategies. Without proper evaluation, organizations may miss opportunities for improvement and optimization. Understanding how to gauge collaboration efficacy is essential not just for strategic planning but also for maintaining and enhancing supplier relationships. When collaboration is measured accurately, how organizations perform can be highlighted, and areas needing attention can be identified.
Effective supplier collaboration contributes to long-term success. It leads to reduced costs, improved efficiency, and innovative solutions. Measuring collaboration success reveals how well these objectives are being met. This process includes identifying measurable metrics, tracking performance over time, and making informed decisions based on data-driven insights.
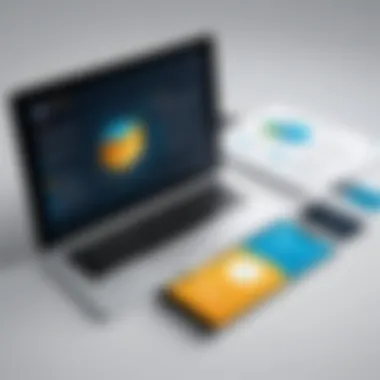
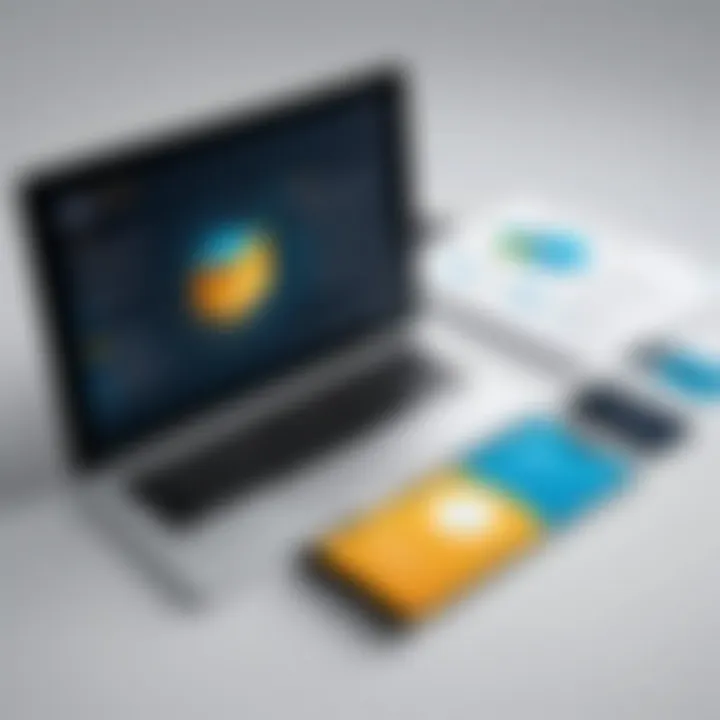
Investing time in this aspect of supplier collaboration fosters a culture of trust and transparency. Organizations can align their goals with suppliers. Establishing clearly defined metrics ensures that both parties share a mutual understanding of expectations, responsibilities, and performance.
Establishing Key Performance Indicators (KPIs)
Defining Key Performance Indicators is one of the first steps in measuring collaboration success. These KPIs serve as quantifiable metrics that help assess the effectiveness of supplier relationships. It is vital to select KPIs relevant to specific objectives and aligned with broader business goals.
Common KPIs for supplier collaboration include:
- On-Time Delivery Rate: Measures the percentage of shipments received on time. A high rate indicates reliability in the supply chain.
- Quality Performance: Assesses the quality of goods received in line with expectations. Poor quality can lead to increased costs and diminished productivity.
- Cost Savings: Evaluates the impact of negotiation strategies and collaboration on overall spend. Organizations must identify tangible financial benefits.
- Supplier Responsiveness: Measures how quickly suppliers respond to requests and address issues. High responsiveness indicates a proactive approach to problem-solving.
By establishing these KPIs, organizations can create benchmarks for performance. They allow the tracking of improvements over time, thus ensuring that collaboration efforts remain aligned with organizational priorities.
Tools for Monitoring Performance
Monitoring performance effectively requires reliable tools that can track KPIs in real time. With various options available, organizations can choose based on their existing infrastructure and specific needs.
Some valuable tools for performance monitoring include:
- SAP Analytics Cloud: This tool offers real-time insights and data visualization features. It helps in tracking KPIs and informs decision-making processes.
- Power BI: Microsoft Power BI provides interactive reporting capabilities that allow for the analysis of supplier performance in an easy-to-understand format.
- Supply Chain Management Software: Many comprehensive solutions contain built-in monitoring capabilities. These solutions integrate directly with existing operations, providing a holistic view of supplier performance.
These tools should be implemented with a clear understanding of the KPIs established earlier. They provide the platform for ongoing monitoring and adjustments based on real-time data.
Regular reviews of performance metrics and engaging discussions with suppliers can lead to beneficial adjustments and enhancements in collaboration strategies.
Future Trends in Supplier Collaboration
The landscape of supplier collaboration is rapidly evolving due to technological advancements. Understanding future trends is essential for organizations aiming to maximize efficiency and build better supplier relationships. This section will focus on two specific trends: the impact of artificial intelligence and blockchain technology. Each plays a crucial role in enhancing supplier collaboration.
The Impact of Artificial Intelligence
Artificial intelligence (AI) is set to transform supplier collaboration significantly. By using AI, companies can analyze vast amounts of data to forecast demand and optimize inventory management. AI algorithms can identify patterns in supplier performance, which helps in making informed decisions.
Some specific benefits of implementing AI in supplier collaboration include:
- Enhanced Decision-Making: AI provides deeper insights into supplier capabilities and risks, allowing companies to choose the right partners for their projects.
- Automation of Routine Tasks: Many mundane tasks in supplier management, such as invoice processing and order tracking, can be automated through AI solutions. This leads to increased efficiency.
- Predictive Analytics: AI can analyze historical data to predict future outcomes, which is beneficial for demand planning and supply chain forecasting. This ensures that organizations are well-prepared to meet market demands.
Adopting AI does come with considerations. Companies need to be mindful of data privacy and the quality of data they input. With proper governance, AI can lead to more proactive supplier management and stronger partnerships.
Blockchain and Supplier Transparency
Blockchain technology provides a solution for enhancing transparency and accountability in supply chains. It creates a secure, tamper-proof ledger that records every transaction between suppliers and organizations.
Benefits of using blockchain for supplier collaboration include:
- Improved Traceability: Every transaction can be tracked, making it easier to identify the origin of materials and verify the ethical practices of suppliers.
- Reduced Fraud: With its secure nature, blockchain minimizes fraud risks. Organizations can trust the information provided without the need for intermediaries.
- Faster Dispute Resolution: In case of conflicts, blockchain can provide clear evidence of transactions, reducing the time taken to resolve issues.
Implementing blockchain requires careful thought. Organizations must consider the technological infrastructure and train staff to use this technology effectively. However, the long-term benefits can lead to stronger relationships and trust among suppliers, ultimately enhancing collaboration.
"The use of AI and blockchain is not just about technology; it's about reshaping the relationships between organizations and their suppliers, enabling collaboration that is more efficient and transparent."
Epilogue
Supplier collaboration is integral to the success of organizations today. This article emphasizes the various facets of collaboration enabled by SAP solutions. Maximizing supplier collaboration through these tools allows firms to streamline their supply chain processes effectively, ensuring that they remain competitive in their respective markets.
Summary of Key Points
Several critical points emerge from the discussion:
- Importance of Collaboration: Effective collaboration with suppliers can lead to significant operational efficiencies and cost reductions.
- SAP Solutions: The SAP ecosystem offers robust tools, such as Supplier Relationship Management (SRM) and Materials Management (MM), which facilitate smoother interactions and data sharing.
- Benefits of Enhanced Collaboration: Improved responsiveness, deeper relationships with suppliers, and the ability to adapt to market changes are vital advantages that come from utilizing SAP solutions.
- Implementation Steps: Properly assessing existing processes, integrating supplier data, and training internal teams are essential steps in successfully adopting SAP for supplier collaboration.
- Future Trends: Emerging technologies, particularly AI and blockchain, are set to revolutionize the way organizations interact with suppliers.
Call to Action for Organizations
To thrive in today's competitive landscape, organizations must recognize the strategic importance of maximizing supplier collaboration. It is not merely about having good relationships but also about leveraging technology to derive tangible benefits. Here are some steps organizations can take:
- Assess Current Collaboration Practices: Evaluate existing supplier relationships and identify areas for improvement.
- Invest in SAP Solutions: Consider implementing or upgrading SAP tools that encourage collaboration.
- Engage with Suppliers: Foster open communication channels and seek their input during technology transitions.
- Monitor and Measure Success: Use established KPIs to track the performance of collaborations and adjust strategies accordingly.
- Stay Informed About Trends: Keep abreast of technological advancements that can enhance collaboration.
By following these steps, organizations can foster stronger partnerships with suppliers, thereby creating a more resilient supply chain that delivers lasting value.