Exploring Digital Quality Management Systems
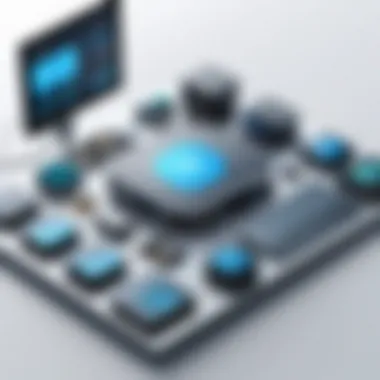
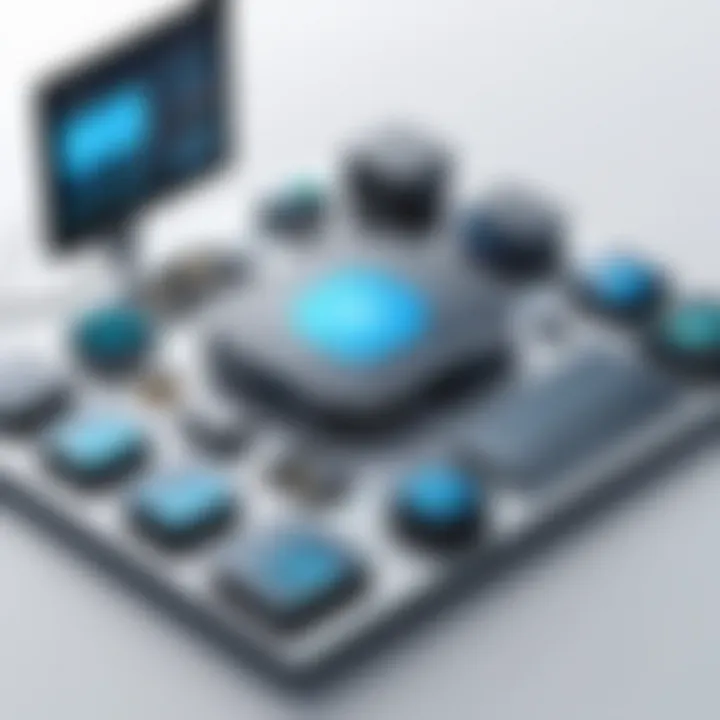
Intro
In todayβs fast-paced business environment, Digital Quality Management Systems (QMS) have emerged as an essential tool for organizations seeking to maintain quality and compliance. This article aims to explore the different facets of Digital QMS, shedding light on their mechanisms, advantages, and role in improving processes.
A digital QMS integrates diverse functions to streamline quality-related tasks. It minimizes paper usage and automates workflows, making quality management efficient and data-driven. The result is an enhancement in quality assurance, operational efficiency, and compliance with regulatory standards.
Overview of Software
Description of Software
Digital Quality Management Systems consist of software platforms designed to facilitate the management of quality processes within organizations. These systems offer a centralized repository to track documents, processes, non-conformities, and corrective actions. They cater to various sectors, including manufacturing, healthcare, and service industries.
Key Features
The principal features of a Digital QMS include:
- Document Control: Ensures that all quality documents, such as policies, procedures, and work instructions, are current and accessible.
- Audit Management: Facilitates internal and external audits by scheduling, managing findings, and generating reports.
- Risk Management: Helps identify, assess, and mitigate risks affecting product quality and compliance.
- Training Management: Tracks employee training and ensures that staff are qualified to perform their roles effectively.
- Reporting and Analytics: Offers insights through data analysis, enabling informed decision-making and continuous improvement
Digital QMS provides a structured approach to quality management, rooted in data and focused on continuous enhancement.
Software Comparison
Comparison with Similar Software
Many software options exist in the market. Systems such as MasterControl and ETQ Reliance provide similar functionalities. However, the choice of system can depend on the specific requirements of an organization, such as scalability, user interface, and sector compatibility.
Advantages and Disadvantages
Digital QMS comes with several advantages, including:
- Enhanced Efficiency: Reduces paperwork and manual processes, allowing teams to focus on core activities.
- Better Data Management: Centralized data storage makes access easier and improves collaboration.
- Improved Compliance: Automated tracking of compliance helps organizations meet regulatory requirements consistently.
However, challenges may arise:
- Implementation Costs: Initial setup and training may require significant investment.
- User Adoption: Employees may resist switching from familiar systems to a digital platform, impacting overall efficiency.
In summary, a Digital QMS offers a structured and efficient approach to managing quality, but organizations must evaluate both its benefits and drawbacks before adopting these systems.
Prolusion to Digital Quality Management Systems
Digital Quality Management Systems (QMS) are becoming increasingly important in todayβs fast-paced business environment. The move from traditional, paper-based systems to digital platforms represents a fundamental shift in how organizations manage quality. This transition is guided by the need for improved efficiency, data accuracy, and compliance across various industries. In essence, Digital Quality Management Systems streamline quality assurance processes, enhance collaboration among teams, and facilitate real-time reporting and analysis.
Definition and Overview
A Digital Quality Management System is a software solution designed to document, track, and manage quality control processes. It integrates various tools that allow organizations to monitor their internal processes more effectively. Typically, a QMS encompasses features such as document management, auditing, compliance tracking, and corrective actions.
These systems not only help maintain high standards of quality but also support the continual improvement of processes, which is essential for organizational growth. Implementing a digital approach allows companies to utilize data for informed decision-making, a stark contrast to the limitations of manual processes.
Importance of a Digital QMS
The importance of a Digital QMS lies in its ability to minimize risks associated with quality management. Companies face increasing pressure to comply with regulatory standards and to provide value to their customers. A digital system can enhance accountability by providing a transparent view of quality metrics and compliance throughout the organization.
Moreover, having real-time access to quality data empowers teams to address issues promptly. With a digital system in place, organizations benefit from reduced errors, improved collaboration across departments, and better customer satisfaction. The investment in a Digital Quality Management System serves as a strategic move toward operational excellence and continuous improvement.
"Digital Quality Management Systems not only assure quality but also bolster organizational agility and responsiveness to market changes."
By recognizing the value of Digital QMS, businesses can position themselves to meet not only current demands but also anticipate future challenges.
Key Components of Digital QMS
The Key Components of Digital Quality Management Systems (QMS) are vital to understanding how these systems function and provide value. Each component represents a fundamental building block that contributes to efficient and effective quality management in organizations. Incorporating these elements allows firms to streamline processes, maintain compliance, and drive quality improvements.
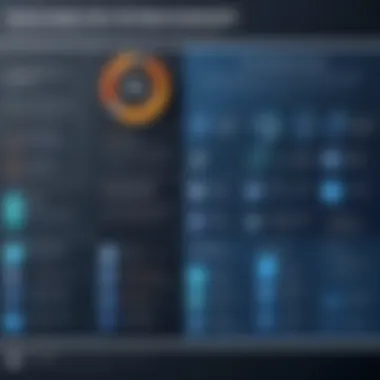
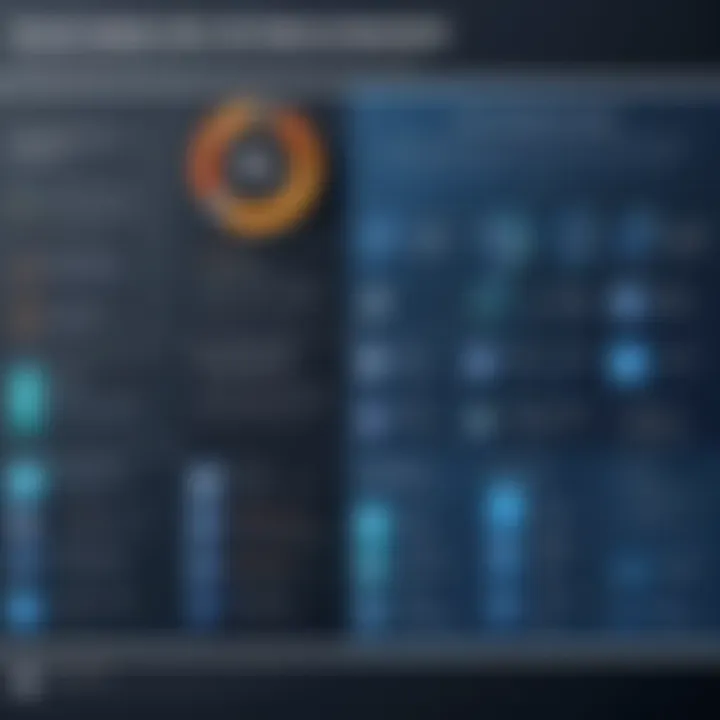
Document Management
Document management forms the backbone of any digital QMS. It is essential for handling the influx of documents that arise from policies, procedures, and standards. Effective document management ensures that all documentation is organized, accessible, and easily retrievable. This is critical in industries where compliance is paramount. A digital QMS facilitates version control, where the most current documents are readily identified, reducing risks associated with outdated or incorrect information.
Additionally, automation within document management helps eliminate manual errors and saves time. Users can quickly search, edit, and distribute documents as needed, which enhances efficiency. By adopting a digital document management system, organizations enhance their capability to manage knowledge effectively, ultimately supporting overall business objectives.
Non-Conformance Management
Non-conformance management is about identifying and addressing deviations from expected standards or processes. A digital QMS enables organizations to capture non-conformance events accurately and efficiently. By documenting these instances, companies can analyze trends and root causes, allowing for informed decision-making on whether corrective actions are needed.
Handling non-conformance promptly minimizes risks associated with potential quality failures. Digital tools often include workflows that facilitate timely responses to non-conformance reports. This responsiveness is crucial for maintaining customer trust and ensuring that quality standards are upheld consistently.
Corrective and Preventive Actions (CAPA)
Corrective and Preventive Actions, or CAPA, is a systematic approach to address issues. Corrective actions focus on resolving immediate problems, while preventive actions aim to eliminate root causes to avoid future issues. In a digital QMS, CAPA is streamlined through integrated processes that ensure issues are tracked, analyzed, and resolved.
Effective CAPA mechanisms can significantly reduce the likelihood of recurrent problems. With a digital tool, organizations can maintain a clear audit trail of actions taken, which is essential for compliance and continuous improvement efforts. These features help organizations not only respond to current challenges but also proactively prevent future quality issues.
Auditing and Compliance Tracking
Auditing and compliance tracking within a digital QMS are crucial for ensuring that organizational processes meet established standards and regulations. Digital systems facilitate regular audits by providing tools for scheduling, conducting, and documenting audit findings. This automation enhances accuracy and reduces the time required for manual audits.
Compliance tracking is equally important. With regulations constantly evolving, organizations need to stay updated and adapt their processes accordingly. A digital QMS helps in monitoring compliance through real-time data, alerts, and reporting features. This enables organizations to respond quickly to regulatory changes, minimizing risks and ensuring adherence to quality standards.
Maintaining a strong audit and compliance tracking system is not just about meeting regulations; it is about fostering a culture of quality across the organization.
Implementing a Digital Quality Management System
The integration of a Digital Quality Management System (QMS) within an organization is a critical endeavor. It underscores how quality management practices can be transformed through the use of technology. A systematic approach to implementing a digital QMS can yield significant gains in efficiency, compliance, and overall organizational performance. This section will delve into key aspects that include assessing organizational needs, selecting appropriate software, and managing the crucial training processes involved in the transition.
Assessing Organizational Needs
Understanding the specific requirements of a business is the first step in implementing a digital QMS. Every organization has unique quality challenges and operational workflows that must be considered. A thorough assessment involves evaluating existing processes, identifying gaps, and defining quality objectives. This helps in establishing a foundation for the QMS.
Key factors in assessing needs include:
- Current Quality Issues: Analysis of ongoing problems and how they impact operations.
- Stakeholder Requirements: Gathering input from all levels to ensure the system meets diverse needs.
- Regulatory Compliance: Understanding relevant regulations that necessitate specific features in the software.
By clearly defining these elements, businesses can ensure the digital QMS aligns with both operational goals and compliance requirements.
Selecting the Right QMS Software
Once the needs are established, the next step is to choose a software solution that is suitable for those requirements. The right QMS software plays a pivotal role in ensuring successful quality management. Some essential considerations include:
- Usability: The software should be user-friendly to encourage adoption across the organization.
- Scalability: It must accommodate future growth and changes within the business.
- Integration Capabilities: Compatibility with existing systems to avoid disruptions during implementation.
- Vendor Support: A reliable vendor that offers ample support and guidance can make the transition smoother.
Each business must evaluate potential software solutions based on these criteria. A comprehensive approach helps ensure that the selected software truly supports the organizationβs quality management objectives.
Training and Change Management
Effective training and change management are crucial in the successful adoption of a digital QMS. Staff need to understand how to use the new system effectively. Without proper training, even the best software can fail to deliver the expected results.
Key steps in managing this process include:
- Developing Training Programs: Tailor training sessions for different roles, ensuring relevance to daily tasks.
- Encouraging Feedback: Create a feedback loop where employees can share insights about the system's effectiveness.
- Promoting Cultural Change: Foster a culture that embraces change and continuous improvement in quality practices.
Change management goes beyond training; it is about shifting mindsets. Engaging with employees and addressing concerns will help ease the transition.
"The key to successful implementation is not just technology; it is about creating an environment where quality is valued and continuously improved."
In summary, carefully implementing a digital QMS is a complex but rewarding journey. By addressing organizational needs, selecting suitable software, and facilitating effective training, businesses can enhance their quality management practices for sustainable success.
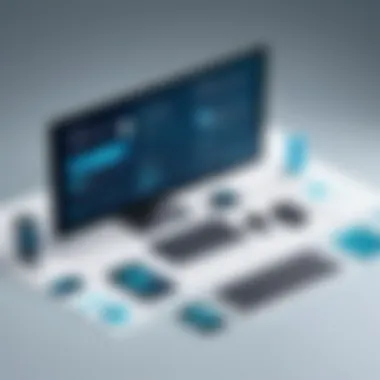
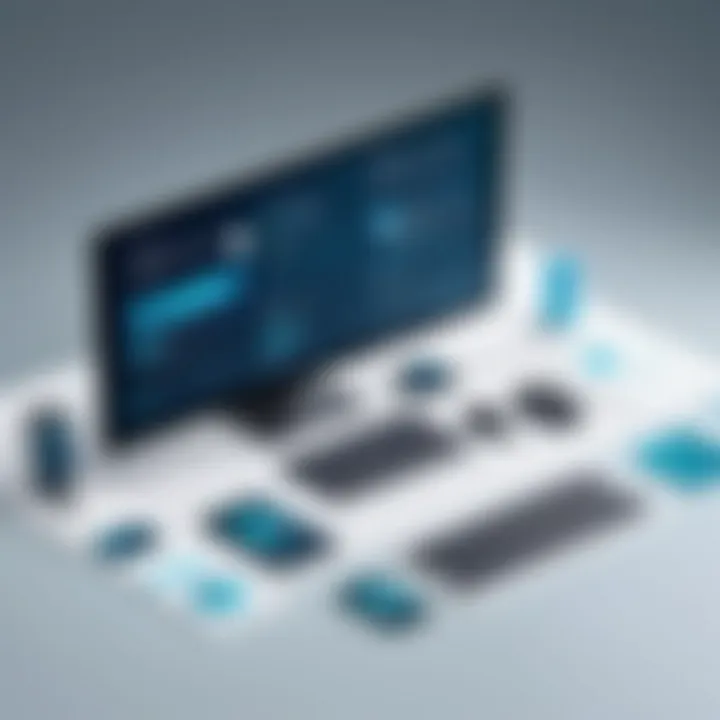
Benefits of Digital QMS
Digital Quality Management Systems (QMS) play a crucial role in modern organizations. Their impact is significant across various sectors, seeking to enhance operational performance and compliance. Understanding the benefits of a Digital QMS is essential for organizations aiming to improve their quality management efforts.
Enhanced Efficiency
Enhanced efficiency is one of the most notable advantages of integrating a Digital QMS into existing processes. Manual paper-based systems are often slow and prone to errors. Digital systems streamline workflows through automation and standardized processes. Tasks such as document management, audit trails, and corrective action workflows benefit immensely from technology.
For instance, when a non-conformance occurs, the resolution process is accelerated by automated notifications to responsible personnel. This not only saves time but prevents quality issues from dragging on, allowing organizations to focus on their core competencies. With a Digital QMS, employees are empowered to complete their tasks more effectively, which can lead to increased productivity and overall satisfaction.
Improved Compliance and Risk Management
Compliance with regulatory requirements is non-negotiable for many industries. A Digital QMS supports organizations in maintaining compliance with established guidelines and standards. By facilitating real-time monitoring and reporting, these systems provide transparency in operations. This transparency helps in building trust with stakeholders and reduces the risk of non-compliance.
Moreover, risk management becomes more structured. Organizations can identify, analyze, and mitigate risks with greater ease. Digital QMS solutions often include features for risk assessment and management, allowing businesses to maintain a proactive stance rather than being reactive. By generating reports that track compliance performance, organizations can readily identify areas needing improvement, ensuring continuous growth.
Real-Time Data Analysis and Reporting
Data-driven decision-making has never been more critical. A Digital QMS enables organizations to collect, analyze, and report data in real-time. This capability allows businesses to visualize their performance metrics and quality trends, leading to timely interventions when necessary.
With real-time reporting, organizations can access dashboards that present key performance indicators. This access allows stakeholders to make informed decisions based on up-to-date information. A continuous feedback loop aids in identifying performance gaps and areas for quality enhancement. Furthermore, timely reporting can also facilitate regulatory audits, where accurate documentation is essential.
According to a study, organizations with a digital QMS see a significant decrease in compliance violations by up to 30% due to effective monitoring and reporting mechanisms.
In summary, the benefits of Digital QMS are evident through enhanced efficiency, improved compliance and risk management, and robust real-time data analysis. These systems serve as a backbone for organizations seeking to optimize their quality processes and ensure sustainable operational excellence.
Challenges in Transitioning to Digital QMS
Transitioning to a Digital Quality Management System (QMS) can be a multifaceted endeavor. Understanding the challenges involved is crucial for achieving success. Each challenge can impact the overall efficiency and effectiveness of the implementation process. Addressing these obstacles thoughtfully can lead to improved outcomes.
Resistance to Change
One significant challenge in the transition is resistance to change within the organization. Employees may feel uncertain about adapting to new technologies and processes. This resistance can stem from various factors. Some may fear loss of job security, while others may simply prefer established methods over new digital systems.
To mitigate this resistance, it is vital to foster an organizational culture that embraces innovation. Clear communication regarding the benefits of a Digital QMS is essential. Educating team members about how these systems enhance work efficiency can alleviate fears. Involving employees in the process also encourages acceptance. Listening to their concerns helps to create an environment of collaboration.
Data Security Concerns
Data security issues pose another challenge when transitioning to a Digital QMS. Companies deal with sensitive information, making it imperative to ensure data integrity and confidentiality. Concerns about data breaches or unauthorized access can hinder the adoption of new systems.
Organizations must emphasize the importance of robust security measures during implementation. Choosing reputable software vendors who provide strong cybersecurity protocols is essential. Regular training for staff on data protection practices should also be a priority. This proactive stance builds trust among employees about the security of the new system.
Integration with Existing Systems
The integration of a Digital QMS with existing systems can complicate the transition process. Many organizations operate with legacy systems that may not be compatible with newer software. This can lead to fragmentation of data and operational inefficiencies.
A carefully structured integration plan is critical. Companies should conduct a thorough assessment of their current systems before making changes. Identifying potential gaps or areas of overlap is vital to successful integration. Engaging IT professionals during this phase ensures compatibility, leading to a cohesive management system.
Effective integration can streamline operations and enhance data usage across the organization. This, in turn, supports accurate reporting and informed decision-making.
Industries Benefiting from Digital QMS
Digital Quality Management Systems (QMS) are becoming essential across various sectors. They address unique challenges and enhance operational efficiency, compliance, and quality control. This section explores how different industries gain from adopting a digital QMS, highlighting specific benefits and considerations.
Healthcare
In the healthcare sector, digital QMS plays a crucial role. The industry faces strict regulatory requirements. A digital QMS helps ensure compliance with standards set by organizations like the FDA and CMS. By standardizing procedures, hospitals and clinics can improve patient safety and reduce errors in medication administration and treatment protocols.
Benefits of using a digital QMS in healthcare include:
- Streamlined Documentation: Digitizing records minimizes paperwork and helps in quicker retrieval of patient information.
- Enhanced Tracking of Compliance: Automated tracking of regulatory standards can save time and improve adherence to protocols.
- Data Integrity and Security: Digital systems can enhance the protection of sensitive patient information, reducing risks associated with data breaches.
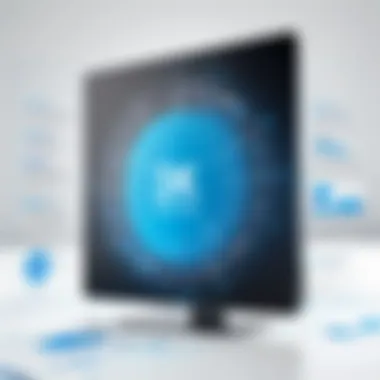
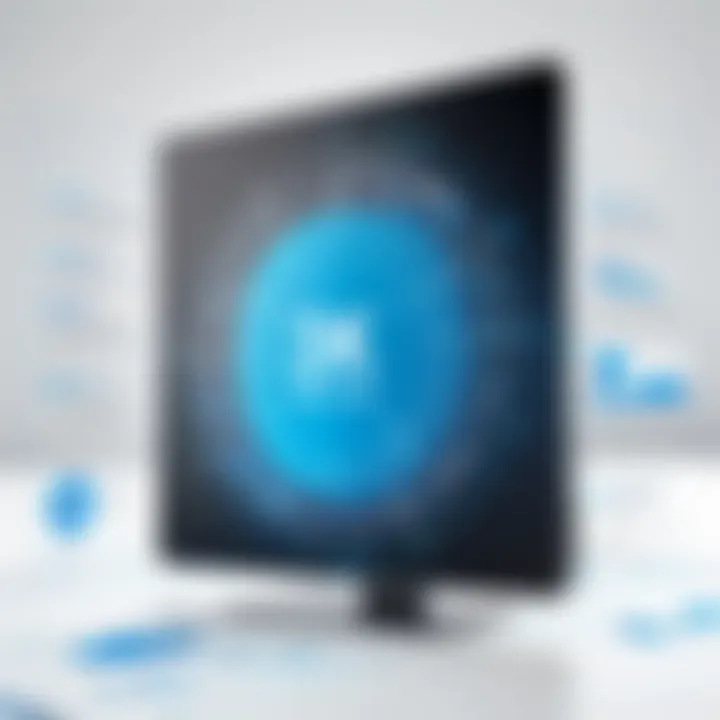
"Implementing a digital QMS can reduce human errors and enhance patient outcomes."
Thus, a robust digital QMS can significantly impact healthcare delivery.
Manufacturing
The manufacturing industry is characterized by complexity and the need for strict quality control. Digital QMS solutions enable manufacturers to maintain high standards while improving operational efficiency. They facilitate monitoring of production processes, ensuring that production complies with industry standards.
Key advantages of digital QMS in manufacturing involve:
- Process Optimization: By tracking production workflows, companies can identify inefficiencies and areas for improvement.
- Quality Assurance: Digital quality management aids in regular audits and inspection processes, ensuring that products meet predetermined quality standards.
- Regulatory Compliance: Similar to healthcare, the manufacturing sector must meet various regulations. A digital QMS assists in recording data and ensuring compliance, reducing the risk of penalties.
Manufacturers benefit greatly from adopting such systems in maintaining product integrity and customer satisfaction.
Pharmaceuticals
The pharmaceutical industry operates under stringent regulations due to the nature of its products. A digital QMS is invaluable in this sector for several reasons, including safety, efficacy, and compliance. These systems ensure that every process, from drug development to production, adheres to regulatory requirements.
Notable benefits of implementing a digital QMS in pharmaceuticals include:
- Traceability: A digital QMS ensures each step of the production process is documented, enabling traceability in the event of recalls or safety issues.
- Risk Management: Digital solutions help identify and mitigate risks associated with drug production and distribution.
- Improved Collaboration: A centralized QMS fosters collaboration across teams, ensuring that everyone is aligned with quality objectives.
The pharmaceutical sector can further improve its response to regulatory changes through a well-implemented digital QMS.
Future of Digital Quality Management Systems
The landscape of Digital Quality Management Systems (QMS) is evolving at a rapid pace. Understanding the future of these systems is vital for organizations aiming to maintain competitiveness and ensure compliance. The increasing reliance on technology in quality management drives the need for more sophisticated solutions. As businesses pursue operational excellence, awareness of emerging trends and capabilities becomes essential.
Trends Shaping the Industry
Several trends are currently influencing the direction of Digital QMS. Here are some notable ones:
- Cloud-Based Solutions: Cloud technology is making quality management more accessible. Organizations can deploy QMS without extensive infrastructure investments, allowing even small businesses to benefit.
- Data Analytics: The integration of advanced analytics tools allows organizations to make data-driven decisions. Analyzing trends and performance metrics helps in identifying areas for improvement.
- Mobile Technology: The use of mobile applications for QMS promotes real-time data entry and access. This flexibility supports a more dynamic approach to quality management, especially in industries like manufacturing.
- Regulatory Compliance Automation: Automating compliance tasks reduces manual errors and enhances tracking. This is particularly beneficial in industries subject to strict regulations, ensuring organizations stay compliant with minimal effort.
"The integration of new technologies in Quality Management Systems can lead to significant operational improvements, shaping the future landscape of industries."
These trends indicate a commitment to agility and efficiency in quality management practices. Organizations embracing these shifts will likely see substantial improvements in compliance and performance.
The Role of Artificial Intelligence
Artificial Intelligence (AI) is gradually transforming how organizations approach quality management. The adoption of AI introduces several advantages:
- Predictive Analytics: AI enables predictive modeling, allowing companies to foresee potential quality issues. This proactive approach minimizes risks before they escalate, ensuring consistent product and service quality.
- Process Optimization: AI algorithms help streamline quality processes by identifying inefficiencies. By automating routine tasks, organizations can focus on strategic initiatives.
- Enhanced Reporting: AI-powered systems can generate insightful reports with minimal human input. This provides greater visibility into quality indicators, empowering teams to make informed decisions swiftly.
AI holds the potential to revolutionize Digital QMS. As capabilities evolve, organizations willing to harness these technologies will likely lead the industry in quality management efficiency. This shift emphasizes the importance of continuous learning and adaptability in the workforce.
In summary, the future of Digital Quality Management Systems is defined by technological advancements and a focus on proactive strategies. By understanding and implementing these trends and technologies, organizations can position themselves for long-term success. The embrace of these innovations not only enhances compliance and performance but also fosters a culture of continuous improvement.
The End
In the realm of Digital Quality Management Systems, the conclusion serves as a pivotal point that encapsulates the overarching themes presented in this article. It highlights the significance of implementing a robust QMS and the tangible benefits it offers to organizations.
Summary of Key Insights
Digital Quality Management Systems are integral for enhancing organizational efficiency and compliance. Key insights from this discussion include:
- Enhanced Data Management: Digital QMS simplifies documentation processes, making access and retrieval straightforward.
- Real-Time Monitoring: These systems allow organizations to monitor quality metrics in real-time, leading to quicker response times in decision-making.
- Improved Collaboration: Teams across different departments can work more effectively, fostering a culture of continuous improvement.
- Regulatory Compliance: Adhering to industry standards becomes less burdensome, as the software often integrates compliance checks throughout the workflow.
These elements reinforce the importance of embracing a digital QMS to remain competitive and maintain high-quality standards in every aspect of operation.
Final Thoughts on Digital QMS
The future trajectory of Digital Quality Management Systems appears promising, with increasing advancements in technology influencing their development. Organizations must recognize that successful implementation requires not only the right software but also a commitment to cultural change within the company. Investing time in training staff and addressing resistance to change can catalyze effective integration of the QMS.
As industries evolve, the role of digital QMS will likely expand, incorporating more advanced features such as artificial intelligence and data analytics. Therefore, organizations should stay ahead by continually updating their systems to harness these innovations for sustained excellence in quality management.
Quality management is not static; it evolves. Adopting a digital QMS enables businesses to adapt to these changes proactively, ensuring that they remain leaders in their respective fields.