NX Simulation: Key Features and Benefits Explained
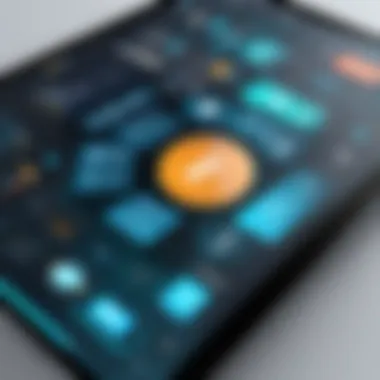
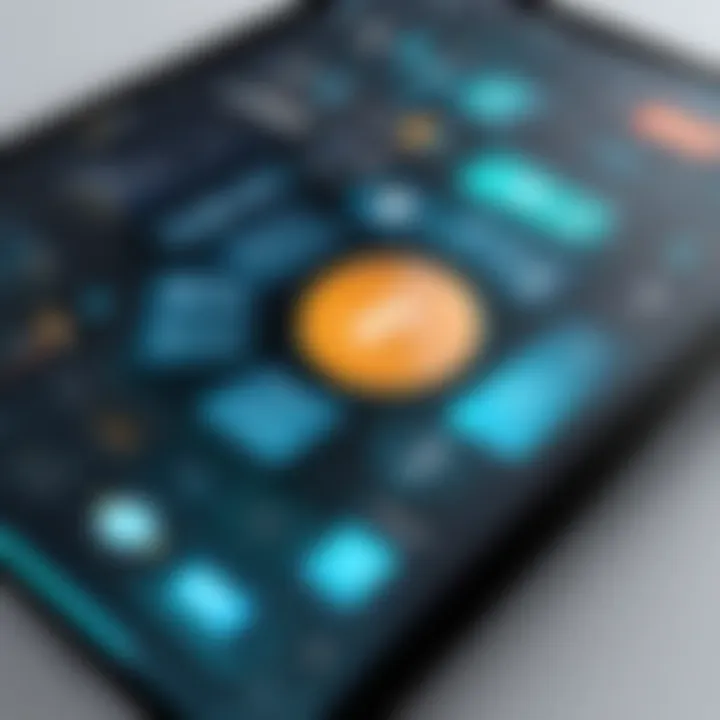
Intro
The landscape of engineering design is rapidly changing, with simulation tools taking center stage in the quest for efficiency and precision. Among these, NX Simulation stands out as a robust software that enables engineers to craft intricate designs and evaluate their performance under varying conditions. This introduction sets the stage for a comprehensive exploration of NX Simulation, breaking down its extraordinary capabilities, key features, and its critical role in modern engineering workflows.
Whether working on complex automobiles or intricate aerospace components, the need for reliable simulation tools cannot be overstated. NX Simulation offers professionals the chance to test and refine designs even before physical prototypes are made, thereby saving both time and resources. As we dive deeper, we will uncover how this software integrates seamlessly into engineering processes, fostering innovation and facilitating informed decision-making across various industries.
In this article, we will dissect NX Simulation's core offerings, compare them with other tools in the market, and elucidate the advantages and challenges associated with its use. This narrative aims to provide a clearinghouse of information for IT and software professionals, equipping them to assess the software's value in their specific contexts.
As the saying goes, "An ounce of prevention is worth a pound of cure." In engineering, this translates into the necessity of simulating to predict performance and mitigate risk, making NX Simulation not just a tool, but an essential asset in today's competitive environment.
Preface to NX Simulation
In today's fast-paced engineering and manufacturing environment, simulation tools like NX Simulation have become indispensable. Their ability to predict real-world performance before production mitigates risks and optimizes design processes. From assessing product durability to analyzing fluid dynamics, NX Simulation provides a platform for engineers to explore design choices with confidence. This section probes into the definition and historical backdrop of NX Simulation, laying a foundational understanding for the discussions that follow.
Definition of NX Simulation
NX Simulation refers to a suite of advanced simulation capabilities embedded within the NX software environment. It incorporates various analytical tools that facilitate tasks such as Finite Element Analysis (FEA), Computational Fluid Dynamics (CFD), and optimization functionalities. Essentially, NX Simulation allows engineers to virtually test and refine their designs, minimizing potential flaws and enhancing overall product performance.
Key aspects of NX Simulation include:
- Finite Element Analysis (FEA): Offers insights into stress, strain, and deformation of materials under various loads.
- Computational Fluid Dynamics (CFD): Enables the study of fluid behavior and its effects on products, crucial for industries like aerospace and automotive.
- Optimization Tools: Help modify designs based on performance metrics, striking a balance between functionality and cost.
The importance of leveraging NX Simulation within engineering workflows can't be overstated. Not only does it pave the way for innovative designs, but it also significantly cuts down on trial-and-error phases, fostering efficiency and reducing costs.
Historical Context and Development
To grasp the significance of NX Simulation today, one must look back at its roots. The technology emerged from the evolution of computer-aided design (CAD) in the 1960s, where organizations began to harness computing power for visualizing complex designs. Early iterations of simulation tools focused largely on static load analysis, which were often rudimentary by modern standards.
As advancements in computing technology and algorithms unfolded, simulation integrated more complex mathematical models, allowing engineers to simulate a broad range of conditions. The advent of NX by Siemens in the early 2000s marked a significant leap forward. It combined multiple engineering disciplines into one platform, which laid the groundwork for comprehensive simulation capabilities.
Over the years, NX Simulation has been continuously refined, with the introduction of machine learning and AI-driven algorithms enhancing predictive capabilities. This is especially useful in high-stakes fields such as automotive and aerospace, where performance and safety are paramount.
Understanding the journey of NX Simulation, from a simple analytical tool to a sophisticated suite lends credibility to its application in modern engineering practices. With this foundation established, the article will delve deeper into the core features and functionalities that NX Simulation offers, as well as its applications across various industries.
Core Features of NX Simulation
The effectiveness of NX Simulation lies within its core features, which provide an array of tools designed to aid engineers and designers in analyzing and optimizing their projects. Understanding these functionalities not only enhances one's grasp of the software but also highlights its importance in delivering high-quality designs. The core elements include Finite Element Analysis, Computational Fluid Dynamics, and Optimization Tools, each serves as building blocks that amplify the potential for precision and innovation in engineering solutions.
Finite Element Analysis (FEA)
Finite Element Analysis, commonly referred to as FEA, is a cornerstone feature of NX Simulation that breaks down complex structural problems into manageable elements. By employing this technique, engineers can visualize how components will behave under various conditions. This method is invaluable in ensuring that designs meet safety standards without over-engineering components.
In essence, FEA helps identify potential failure points long before any physical model is constructed. For example, imagine an aerospace engineer tasked with developing a lightweight aircraft wing. Through FEA, the engineer can simulate aerodynamic loads and stress concentrations. The process reveals where reinforcements are necessary, allowing for targeted modifications that optimize material usage without compromising safety.
Computational Fluid Dynamics (CFD)
Next up is Computational Fluid Dynamics or CFD. This feature specializes in simulations dealing with fluid flow, heat transfer, and related phenomenaโcrucial for sectors such as automotive and aerospace. The ability to model and predict fluid behavior can lead to revolutionary design improvements.
Take a racing car design, for instance. CFD enables engineers to analyze airflow over the vehicle's surface and within the engine compartment. By adjusting the shape of body panels or modifying cooling paths based on CFD results, even a small reduction in drag can mean the difference between victory and second place. Itโs this level of precision and foresight that showcases why CFD is integral to NX Simulation.
Optimization Tools
Last but not least, the Optimization Tools in NX Simulation empower users to fine-tune their designs to meet specific performance criteria. These tools aid in balancing various factors, such as material costs, weight, and structural integrity, all while adhering to project constraints.
In practice, an engineer may use optimization algorithms to tweak a bridge's design, reducing material usage without sacrificing stability. These adjustments are often driven by simulations that provide real-time feedback, enhancing the trial-and-error process associated with traditional methods.
"Using NX Simulation's optimization capabilities significantly shortens the design cycle, making the process more efficient and cost-effective."
The combination of these core features not only streamlines workflows but also cultivates an environment where design innovation can flourish. In a world where competitive advantage hinges on efficiency and excellence, users of NX Simulation have at their fingertips the tools necessary to achieve groundbreaking results.
Applications Across Industries
The integration of NX Simulation into various industrial sectors highlights its undeniable significance in modern engineering. Its capability to replicate real-world phenomena allows engineers to develop better products with increased efficiency and reduced costs. Understanding the specific applications across different fields conveys the utility of this software. How each sector utilizes NX Simulation emphasizes crucial elements, offering a perspective on the benefits it introduces, as well as the considerations that need to be factored in based on industry standards and practices.
Aerospace Engineering
Aerospace engineering demands precision due to the vast discussion surrounding safety and performance. NX Simulation plays a critical role here, enabling engineers to conduct thorough analyses on complex structures, such as wings and fuselage designs. By employing techniques like Finite Element Analysis (FEA), engineers can identify potential failure points under varying conditions, be it extreme temperatures or high-speed airflow.
Utilizing NX Simulation, teams can create a digital twin of an aircraft component. This model accurately reflects the physical characteristics and can be altered to test different scenarios without the costs associated with physical prototypes. Such assessments might include:
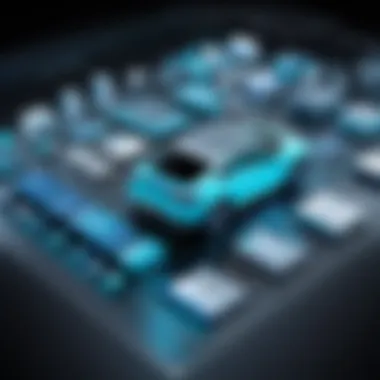
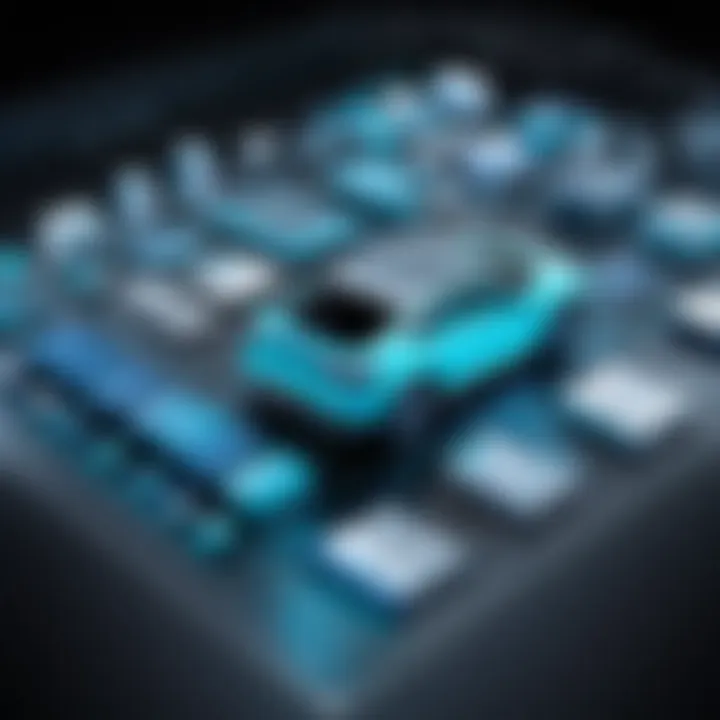
- Aerodynamic performance evaluations: Reviewing how air flows around structures
- Thermal simulation: Understanding how various materials respond to heating and cooling
- Vibration analysis: Ensuring parts can withstand operational resonance
The result is a more streamlined design process, which ultimately leads to enhancements in the safety and efficiency of aerospace vehicles. Overall, NX Simulation stands out as a vital asset, emphasizing not just functionality but essential areas where safety is paramount.
Automotive Sector
In the automotive realm, the stakes are similarly high. The competition to produce effective, safe, and eco-friendly vehicles is fierce. Here, NX Simulation serves as a catalyst for innovation, allowing manufacturers to optimize designs before they hit the production line. The tool assists in simulating crash tests, fluid dynamics, and even the combustion process.
Some key benefits for the automotive industry include:
- Streamlined design revisions: Faster iterations lead to quicker time-to-market
- Cost reductions in physical testing: Virtual simulations reduce the necessity for costly physical prototypes
- Sustainability: Engineers can evaluate materials and processes for environmental impact early in the design phase
The automotive sector can explore designs for everything from engine components to entire vehicle chassis with precision. With accelerated testing capabilities, manufacturers find it easier to comply with regulatory standards, ensuring consumer safety while advancing technological boundaries.
Consumer Product Design
Consumer products face a unique set of challenges, including ever-changing consumer demands and rapid market shifts. NX Simulation becomes an indispensable tool when designers need to validate concepts.\
Through user-centered design approaches, NX Simulation helps in evaluating the ergonomics and functionality of products. It allows designers to:
- Prototype virtually: Collected data from simulations provide valuable insights into user interaction
- Stress test materials and designs: Identifying points of failure before the product reaches the market
- Enhance product aesthetics: Fine-tuning designs based on feedback gathered during the simulation phase
Given the fast-paced nature of consumer goods, leveraging NX Simulation facilitates quick adaptations and refinements of designs based on actual performance metrics. This agility not only enhances customer satisfaction but also promotes a competitive edge in a crowded marketplace.
In summary, the applications of NX Simulation across these industries illuminate how essential it is for modern engineering practice. The software not only supports enhanced design outcomes but also fosters innovation and responsiveness to market needs.
Integration with Other Software Tools
In today's fast-paced engineering environment, the ability to integrate with other software tools is a game changer for NX Simulation. It isn't just a standalone application; it's a part of a larger ecosystem aimed at enhancing productivity and efficiency. You could say itโs like a well-rehearsed orchestra, where each component must play its part harmoniously for the final performance to be outstanding.
This integration allows engineers to streamline their workflows by connecting NX Simulation with various software systems, particularly CAD tools. When the two systems collaborate seamlessly, it accelerates the design process and minimizes the chances for errors. Professionals working in one software can transfer data to another without rework, ensuring that the integrity of the information remains intact.
Collaboration with CAD Systems
Collaboration with CAD systems is perhaps the cornerstone of effective integration in NX Simulation. As designs evolve, timely analysis through simulation becomes crucial. This partnership means NX Simulation can receive 3D models directly from CAD environments like Solid Edge or Autodesk Inventor, allowing for immediate simulation scenarios.
The steps involved can be quite straightforward:
- Model Import: You start with a model in your favored CAD software.
- Direct Transfer: Directly export or link this model to NX Simulation.
- Simulation Setup: Once imported, the simulation parameters can be configured rapidly.
- Real-time Feedback: Any changes made within the CAD system automatically reflect in NX Simulation, enabling real-time results that inform the design iterations.
The beauty of this integration lies in its ability to reduce latency. Engineers can make adjustments on the fly, leading to a more agile design process. Moreover, having a stable interface reduces the cognitive load often associated with switching between different platforms.
APIs and Customization Options
Diving a bit deeper into the tech side, Application Programming Interfaces (APIs) offer a window into extensive customization opportunities. For software professionals, this is a crucial aspect of NX Simulation. Having the ability to create custom scripts or plugins means that users can tailor the software to meet specific needs that might not be covered by the out-of-the-box features.
Consider the following aspects when looking at APIs and customization options:
- Bespoke Functionality: Developers can add new algorithms or modify existing processes, which allows for unique project requirements to be met without waiting for software updates.
- Seamless Integration: APIs support the smooth interaction of NX Simulation with other engineering tools, enhancing functionality and flexibility.
- Automation Scripts: Engineers can develop scripts that automate repetitive tasks, drastically reducing the time spent on mundane activities.
In this landscape, savvy users who take advantage of APIs often find they create a more efficient workflow that enhances their overall experience of NX Simulation. Given the complexity of modern projects, such customizations are not just nice to have; they can be critical in meeting deadlines and maintaining quality.
"Integration with other tools is like the backbone of NX Simulation; it holds everything together and ensures you aren't just working in isolation."
In summary, integrating NX Simulation with other software tools, especially through direct collaboration with CAD systems and utilizing APIs for customization, enhances the usability and efficiency of the overall design and simulation process. Whether it's small tweaks in design or complex re-engineering, the ability to flow smoothly between different platforms ultimately leads to better outcomes in engineering projects.
Workflow in NX Simulation
The workflow in NX Simulation serves as the backbone of the overall simulation process, encompassing the steps necessary to achieve accurate and insightful results. Understanding this workflow is essential for engineers and professionals seeking to optimize their design processes, as it not only facilitates the setup and execution of simulations but also ensures that analyses are aligned with project objectives. Within this section, we will dissect the workflow into three pivotal components: setting up simulations, analyzing results, and employing iterative processes for design improvement.
Setting up Simulations
Setting up simulations in NX is a task that requires precision and a methodical approach. The setup stage lays the foundation for all subsequent analysis, making its importance hard to overstate. Hereโs how it typically unfolds:
- Defining the Geometry: Begin by creating or importing the geometric model of the item you're analyzing. This model should reflect the actual specifications and intricacies of the design.
- Mesh Generation: The quality of the mesh impacts the accuracy of the simulation results. A finer mesh may yield more accurate outcomes but will require more computational power.
- Applying Boundary Conditions: This step involves specifying how the model interacts with its environment. Properly defining these conditions is crucial for ensuring that the simulation reflects real-world scenarios.
- Assigning Material Properties: Each material exhibits unique behaviors under different conditions. Assigning these properties is a vital step that directly influences the simulation accuracy.
By following these steps, users establish a solid groundwork for effective simulation. Attention to detail during this phase can significantly affect overall project timelines and budgets.
Analyzing Results
Once the simulations are complete, the next step is diving into the analysis of results. This phase transforms raw data into actionable insights. Hereโs what typically takes place:
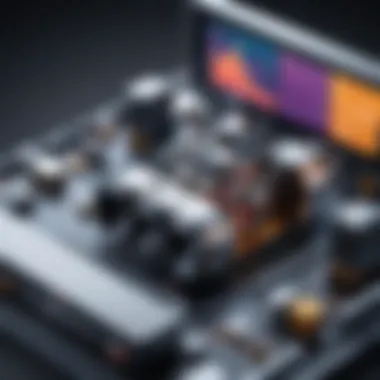
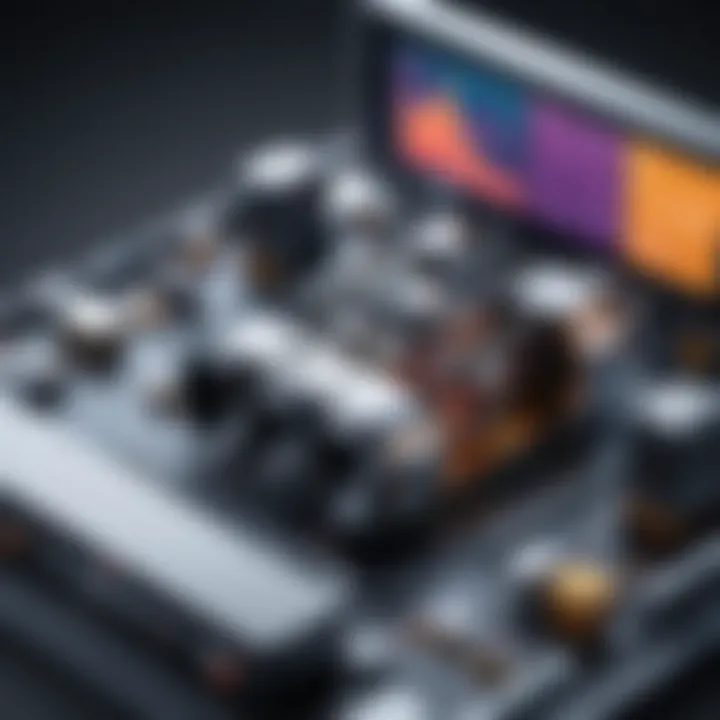
- Visual Inspection: The first glance at results often comes in the form of visual representations such as deformation plots and stress distribution maps. These visuals can highlight problem areas quickly.
- Quantitative Metrics: Engineers will look for specific metrics defined during the setup phase. These include factors like displacement, strain, stress, and factor of safety.
- Comparison with Initial Design Goals: The analysis should reflect whether the design matches the goals set out at the beginning of the simulation process.
Consider this: an analysis is only as good as the assumptions made beforehand. Being detail-oriented here can prevent costly missteps later in the design cycle.
Iterative Processes for Design Improvement
Iteration is where the magic really happens in NX Simulation. This stage is all about refining designs based on analytical insights. Hereโs how to navigate this phase:
- Identifying Weaknesses: Based on the outcomes observed, pinpoint areas requiring enhancement. This could be reducing stress in certain regions or changing material choices.
- Revising the Design: With the weaknesses outlined, engineers modify the existing model. This could range from simple tweaks to more substantial redesigns.
- Re-running Simulations: After changes, it's essential to rerun the simulations to verify improvements. Each iteration should bring the design closer to the desired performance metrics.
- Documentation of Changes: Keeping records of what modifications were made and their impacts can aid in future projects and knowledge retention within teams.
As one dives into the iterative process, itโs crucial to maintain a flexible mindset. What works in theory may not translate directly into practice, making adaptation and re-evaluation necessary components of this workflow.
"The difference between a good engineer and a great engineer lies largely in the iterative process. Continuous improvement is the key to excellence."
User Experience and Feedback
The experience of users while interacting with NX Simulation can significantly impact their workflows and overall satisfaction with the tool. This section explores the feedback from users, focusing on key elements such as interface usability and learning curve, which together shape the perception of the software.
Interface Usability
Interface usability refers to how intuitive and efficient the tool is for users. A well-designed interface is vital as it allows professionals to focus more on their engineering tasks rather than getting bogged down by complicated navigation.
Some aspects that contribute to effective interface usability include:
- Clarity of Layout: An organized layout helps users find essential functions quickly without feeling overwhelmed. This is especially crucial in simulation software where many features are packed together.
- Customization Options: Users appreciate the ability to tailor the interface according to their preferences. NX Simulation offers various customizable features that help set up the workspace in a way that feels natural to the user.
- Accessibility of Tools: Functions, options, and features should be easily accessible. A tool-bar that is cluttered might lead to frustration. Instead, NX Simulation has a strategically designed menu system that helps minimize the time spent looking for specific functionalities.
When users report a positive interface experience, it often translates to better productivity and fewer errors. A simple, streamlined interface allows engineers to perform complex tasks more efficiently.
Learning Curve for New Users
The learning curve is another cornerstone aspect when discussing user experience. For new users, the gap between initial struggles and mastery of the system can determine their long-term engagement. Learning a new simulation tool such as NX can seem daunting, but the challenge can often be mitigated through various considerations.
- Documentation and Tutorials: Comprehensive and well-organized documentation is essential. Users often rely on manuals and online tutorials to get accustomed to the application. NX Simulation provides a wealth of resourcesโboth written and video-basedโto help new users ramp up quickly.
- Community and Support Networks: Engaging with other users through forums, such as on platforms like Reddit, provides a valuable avenue for learning. Community support stands as a crucial factor as it allows novices to share experiences, tips, and tricks that can ease the learning process.
- Interactive Features: The inclusion of interactive tutorials within the software can significantly lower the barrier to entry. These guides often lead users through basic tasks, allowing them to learn by doing rather than just reading.
As highlighted in user feedback, while there may be a steep incline at first, those who invest time into understanding NX Simulation often find that they become proficient more rapidly than expected. The key takeaway here is that a supportive environment fosters success, and NX makes strides to provide that through various means.
"The interface was much clearer than I anticipated, and the guidance helped a lot in those first few weeks. Sometimes, you just need that little nudge to take off!" - User feedback from a recent NX Simulation evaluation.
Advantages of NX Simulation
NX Simulation is not just another cog in the engineering wheel; itโs something that can substantially elevate how professionals design and test their creations. In the fast-paced world of engineering, where the margin for error is slim, having a robust simulation tool can be the difference between success and failure. The advantages of NX Simulation are multifaceted and play a vital role in enhancing engineering practices across sectors. Hereโs a closer look at some of the key benefits these tools provide.
Cost-Effectiveness
One of the most significant advantages of NX Simulation is its potential for cost savings. The initial investment in software and training is often dwarfed by the financial impact of developing prototypes and iterating designs in physical form. With simulation, businesses can explore numerous design variations virtually, identifying the most efficient concepts before any material is ever cut or assembled.
Moreover, using NX Simulation can drastically reduce the need for extensive testing in real-world conditions. Think of it as putting a safety net underneath a tightrope walker. This means companies can allocate funds that would have gone into physical testing to other critical areas, such as R&D or marketing. As a bonus, the findings from simulation can help avoid costly setbacks down the line.
Reduction of Physical Prototyping Needs
Gone are the days when engineering projects required endless prototypes to get the design just right. With NX Simulation, one can create virtual models that replicate physical behavior under various conditions. What does this mean for practice? It means less time spent crafting prototypes and more time refining designs based on simulation results. This is particularly useful in industries like aerospace or automotive, where prototyping can be not only expensive but also time-consuming.
Additionally, the savings extend to materials as well. Not only are fewer prototypes needed, but the materials used for these prototypes don't just vanish into thin air after a test; instead, they can be put to better use. By simulating multiple iterations, teams can hone in on designs that might have taken numerous failed prototypes to find otherwise.
Enhanced Design Insight
NX Simulation doesnโt just speed up the development process; it also enriches the design phase. By providing insights into how a product will behave under realistic conditions, engineers can make more informed choices from the get-go. Simulations can reveal how materials will respond to stress, heat, and other environmental factors before they ever leave the drawing board.
For example, a team working on a new aircraft wing can utilize NX Simulation to see how it will respond to wind forces at various speeds. Rather than relying solely on experience or intuition, they can base decisions on hard data and performance metrics. This kind of in-depth analysis ensures that the final product is not just innovative but also functional and safe.
"In an industry where precision can save lives, understanding design through simulation becomes not just a benefit but a necessity.โ
Ending
The advantages of NX Simulation blend together to create a compelling case for its adoption. From cost-effectiveness to a significant reduction in prototyping needs, coupled with improved design insights, this powerful tool allows engineers to push the boundaries of whatโs possible in design and innovation. As the industry continues to evolve, leveraging these advantages becomes essential for staying ahead in the competitive landscape.
Challenges and Limitations
In every robust system, including NX Simulation, there are inherent challenges and limitations that demand attention. Understanding these can help engineers and developers navigate potential pitfalls while maximizing the software's capabilities. As the field of simulation continues to grow, acknowledging these hurdles becomes crucial for businesses aiming to integrate these tools effectively into their workflows.
Computational Demands
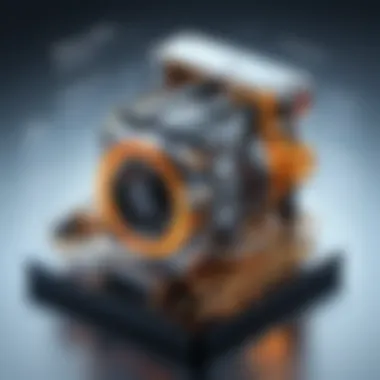
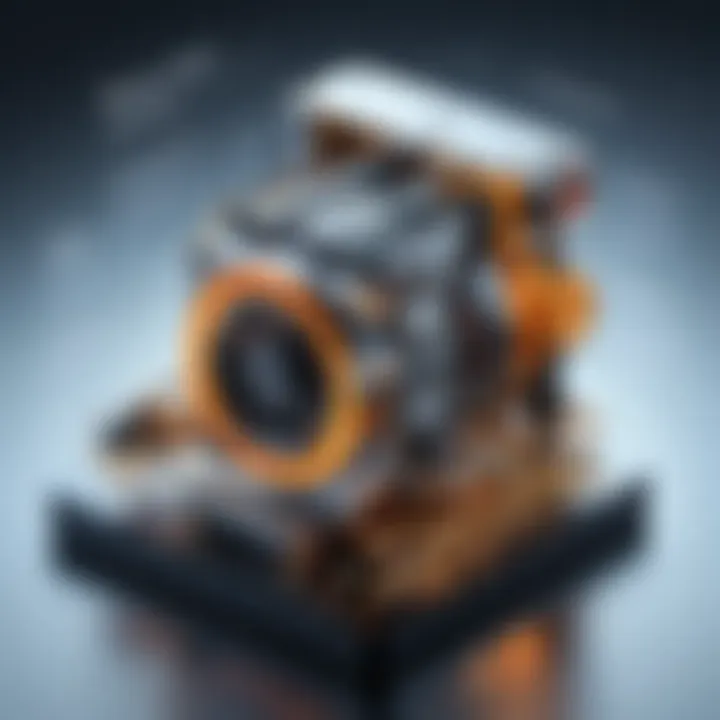
One of the standout features of NX Simulation is its ability to handle intricate calculations and deliver precise results. However, such accuracy comes with a heavy priceโthe demand for significant computational resources.
Users often find themselves needing high-performance computing power to manage complex simulations, especially when dealing with large datasets or detailed multi-physics analyses. This often necessitates investing in high-end servers or cloud computing services. The costs associated with these resources can add up quickly.
Companies must carefully assess their hardware capabilities and model sizes before embarking on extensive simulations. Without the right computational foundation, they risk facing long run times, system crashes, or inaccurate results, which can derail projects and lead to costly delays.
Ultimately, balancing the need for detail with available resources is a continuous challenge in utilizing NX Simulation effectively.
Future Trends in Simulation Technology
As the field of engineering continues to advance, simulation technology is becoming increasingly vital. The future of simulation tools embodies several promising trends that could significantly enhance capabilities and performance. These trends are not just technological upgrades; they also set the stage for innovation across various industries. Understanding these patterns helps professionals align their strategies accordingly, maximizing the benefits of simulation.
Artificial Intelligence Integration
Artificial Intelligence stands at the forefront of transforming simulation technology. By leveraging machine learning algorithms, simulation tools can analyze vast data sets much faster and with greater accuracy than traditional methods. The integration of AI allows for predictive analytics, where simulations can anticipate potential failure points before they occur.
The advantages are manifold:
- Increased Efficiency: AI-driven simulations can run in less time, enabling quicker iterations.
- Enhanced Decision-Making: With predictive capabilities, engineers can make more informed decisions based on potential outcomes.
- Customization: AI can adapt simulations based on previous data, tailoring the experience to meet specific requirements of users or projects.
This trend not only augments existing capabilities but also creates a more intuitive user experience. Engineers can focus on creative problem-solving while AI handles the heavy lifting. The implication for industries is profoundโfewer iterations needed mean reduced costs and faster time-to-market for products.
"The future of engineering design is not just in building better products but in understanding how those products interact with the world using advanced simulations facilitated by AI."
Cloud-Based Solutions and Accessibility
Another significant trend is the shift toward cloud-based simulation solutions. This change to cloud technology introduces a wide array of benefits. Accessibility is the most significant one; professionals can now run simulations from virtually anywhere, whether in the office, out in the field, or remotely. This flexibility fosters collaboration among teams that might be distributed across various geographical locations.
The benefits of cloud-based simulations include:
- Scalability: Users can scale resources depending on project needs without investing heavily in physical hardware.
- Cost-Effectiveness: Subscription-based models usually associated with cloud services can mitigate initial capital expenditures.
- Real-Time Collaboration: Teams can access and work on simulations simultaneously, providing real-time feedback and improving project timelines.
Furthermore, as the cost of cloud storage decreases, more companies are likely to adopt this technology, leading to a more widespread usage of simulation tools among businesses of all sizes.
In summary, the future of simulation technology is bright, with AI integration enhancing accuracy and efficiency while cloud solutions increase accessibility. Understanding and adapting to these trends is crucial for engineers and businesses to stay competitive in an evolving landscape.
Finale and Recommendations
In wrapping up our discussion on NX Simulation, it's clear that the topic holds significant relevance in today's engineering landscape. As the world leans more into intricate designs and demanding analytical requirements, grasping the benefits and practical application of simulation tools becomes essential.
A key element of NX Simulation is its blend of robust features and versatility. Users can harness this tool not just for finite element analysis but also for computational fluid dynamics, making it suitable across various sectors. This begs the consideration: why might one choose to invest time and resources into adopting such a system? The potential returns are numerous, from cost savings on physical prototypes to enhanced design quality. The integration of simulation into the design process allows engineers to identify potential failures and optimize performance long before any physical models are built.
Ultimately, any professional or business looking to improve their engineering processes would benefit from considering NX Simulation. \nReaching a decision, however, requires evaluating not just the pros but also the challenges involved. For instance, the complexity of the software might present a steep learning curve for some users. Recognizing these nuances will ensure a smoother implementation and greater acceptance of simulation workflows.
"Simulation tools are not just a useful addition to your toolkit; they are a necessity for modern engineering."
Summarizing Key Takeaways
To distill the insights shared throughout this article, we can outline the following key points:
- Comprehensive Functionality: NX Simulation encompasses a suite of analytical tools allowing users to run diverse simulations, from stress testing materials to fluid dynamics assessment.
- Industry Relevance: This software isn't restricted to one field; rather, it finds application in aerospace, automotive, and various design sectors.
- Cost-Efficiency and Insight: The capacity to reduce costs related to physical prototyping and operational inefficiencies is a significant advantage.
- Learning Curve and Adaptation: While immensely powerful, the software requires a commitment to learning and adaptation to maximize its full potential.
Suggestions for Implementation
For those contemplating the integration of NX Simulation into their workflow, here are several strategic recommendations:
- Training and Onboarding: Invest in thorough training for your staff. Understanding the capabilities and limitations of the software will unlock its true potential. Consider leaning on online courses or professional tutorials to expedite this process.
- Pilot Projects: Start with pilot projects that enable gradual adoption. This allows teams to gain experience without overwhelming the system or the personnel involved.
- Regular Evaluation and Feedback: Establish a feedback loop among users to consistently refine how NX Simulation is utilized in your workflows. Continuous improvement often leads to uncovering efficiency gains.
- Cross-Functional Collaboration: Encourage collaboration between departments. When engineers, designers, and other stakeholders share insights and learnings from their simulations, it can enhance the overall design process and outcome.
- Stay Updated: Keep abreast of the latest features and updates from the NX Simulation team. The field of simulation is rapidly evolving, and staying informed can provide competitive advantages.
Resources for Further Reading
Resources available for further reading are pivotal for those delving into the world of NX Simulation. This section serves as a treasure trove for engineers, researchers, and professionals who seek to enrich their understanding of simulation technologies and methodologies. The real beauty of these resources lies in their ability to complement theoretical knowledge with practical wisdom, enabling users to apply learned concepts effectively in real-world scenarios.
Books, online courses, and industry publications provide diverse perspectives and in-depth analysis that can profoundly enhance oneโs expertise in NX Simulation. Incorporating a variety of learning formats caters to different preferences, ensuring that all types of learners find something that resonates with them. Whether one prefers the structured format of books or the interactive style of online courses, ample options exist to bridge the gap between knowledge and practical application.
"The best investment you can make is in yourself. The more you learn, the more you earn." - Warren Buffett
Books and Literature
Books and literature represent the backbone of any substantial learning journey, particularly in a complex field like NX Simulation. From comprehensive textbooks filled with key theories to specialized publications focused on niche areas, the literature available covers a wide spectrum of topics. These works provide foundational knowledge as well as advanced insights that can contribute significantly to both novice engineers and seasoned professionals.
Key Benefits of Reading Books on NX Simulation:
- In-depth Knowledge: Books often delve deep into specific aspects of simulation, offering a depth of understanding that shorter articles may lack.
- Credibility and Expertise: Many authors are industry veterans or respected academics, ensuring the content is both credible and informative.
- Reference Material: Reference books can serve as reliable sources for formulas, theories, and case studies that can later be applied in practical situations.
Some recommended reading might include:
- "Finite Element Method: Linear Static and Dynamic Finite Element Analysis" by Thomas J.R. Hughes - An essential read for grasping the theoretical underpinnings of finite element analysis.
- "Introduction to Computational Fluid Dynamics" by Anil W. Date - This book offers a hands-on approach to understanding CFD principles in practical terms.